新设备自动化的进步让钻井工人远离危险区域,从而提高了操作的安全性、可靠性和作业效率。
钻井作业是必不可少的,但本质上存在着危险性,钻井工人每天都面临着各种风险和挑战。从重型设备和移动部件到不可预测的天气条件及其环境状况,钻井平台无疑是钻井作业中最危险的场所。根据IADC(国际钻井承包商协会)2023 年ISP(互联网服务提供商)的报告,钻井作业中损失的时间以及可记录到的人员受伤事故出现最多的场所就是钻台,其中钻工受伤的比例最大。
钻台是一个高强度的工作场所,钻工们必须在该场所的一些危险区域快速安全地执行基本的操作任务,例如安装和拆卸钻杆、管具和套管。钻工们还需相互协作完成起下钻作业,监控和维护重型设备,包括钻机和大钳等设备和工具。然而,钻台上的工作环境十分艰苦、条件苛刻且令人筋疲力尽,但一切工作都必须正确完成。
当然,通过减少钻台上的人机互动,在现场或远程重新定位和认识这方面的专业知识,钻井作业可以做到更安全和更高效。钻井自动化经历了一个长达数十年的探索过程,它不仅能为石油天然气工业带来变革性的环境影响以及运营效率方面的提高,更重要的是,它改变了钻井工人工作的安全环境。
机械化和自动化
2024年7月是 Piper Alpha 生产平台在北海发生爆炸的36周年。这场夺走了167人生命的悲剧促使了全球重新评估安全作业协议。因此,政府机构和行业机构出台了新的、更严格的法律和法规、标准和指南,重点关注的就是安全问题和风险管理。
Piper Alpha生产平台所发生的事故也扮演了一种催化剂的作业,那就是它加速了机械化钻井设备的进步与发展,包括管具操控和管架存放的系统架构。这些大型的重型机械装置帮助海上钻井平台取代了人工操控管具和工具的作业程序,减少了一些危险区域需要人与设备、管具与工具直接接触和操作的要求。虽然这些早期的机械化设备是朝着正确方向迈出的一步,但它们依旧是重型机械,通常需要对钻台进行大的改造,因此,很难改装到现有的钻机上。此外,这些设备的能源密集型特性也给整个钻机底座和基础带来了额外的压力。
随着石油钻井行业的不断发展,NOV(国民油井Varco)公司认识到了需要采取更积极主动的方法来实现钻井自动化。在 2010 年代,该公司开始专注于过程自动化,开发钻井和管具处理解决方案,例如 NOVOS™ 操作平台和多机器控制系统。这些进步通过自动化的重复性动作以及支持多种应用的功能,提高了钻井作业的可靠性和可预测性,使钻井工人能够专注于更关键的任务和作业流程,而不是被手工作业或重复性的工作所困扰。
NOV的最新进展代表了该公司向着自主操控的自动化操作迈出了重要的一步,将自动化和机器人技术集成到钻井工艺流程中,创造出一个非手工操作的钻井平台。该公司的愿景是开发一种全自动化的钻井系统,将设备自动化、过程自动化和态势感知相结合,将当前的设置和设想转变为未来钻机的动作。
钻台设备自动化
钻杆和管具处理是钻台上最常见、最耗时且最容易出现危险的一项工作,需要全体作业人员持续的引起注意,严格按照安全作业程序进行操作。司钻的任务是与钻工们紧密配合,从钻台上的各个位置跟踪钻杆的位置,安全有效地在自身具有联锁装置的各种设备之间将钻杆和管具安装到位、下入井内或拆卸后起出井眼,安放在合适或指定的位置。
同时,司钻还必须注视和查看多个屏幕数据、曲线走势、警报信息以及各种消息,并对工人的安全和来自井筒的数据拥有态势感知能力。与此同时,手工操控钻杆和重型钻铤的井架工也被暴露在井架高位的二层台和各种操作器件中。
自从“Big Foot”在近50年前进入市场以来,铁钻工,又被称作液压大钳(以下简称液压大钳),这种设备使钻井工人能够更轻松、更快速、更安全、更稳健地对钻杆进行上扣和卸扣,将其顺利接入钻具或从钻具中卸开拆下。这种设备的引入不仅提高了操作效率,减少了钻台上的人员伤害,使钻井工人能够脱离险境,还改善了作业体验,减轻了钻井工人接单根、卸单根或起下钻作业上、卸扣操作的身体疲劳。液压大钳还能替代传统的、利用猫头轴对钻杆、钻具进行上卸扣的方法,将一根链绳或棕绳的一端缠绕在钻杆接头上,另一端缠绕在猫头轴上,通过在猫头轴一端拉动链绳或棕绳使钻杆或钻具旋转,使钻杆的公母扣上在一起,并使丝扣上紧。
该行业对大位移水平井和超深井的追求推动了向更大直径钻杆的转变,例如 5
1/
2 in.和 5
7/
8 in.直径的钻杆。虽然大直径钻杆长期以来一直是海上油井的主打产品,但直到最近五年才被引入陆上。这种转变大大增加了对钻机和设备的要求。这些直径更大、井眼更深的井需要能够应对更高扭矩载荷以及能为整个钻具提供更好的重量分布的设备。这些较大直径钻杆的高质量连接需要更强劲的上扣和卸扣扭矩,以及来自顶驱至钻头的增强性扭矩传递,如图1(50多年来,NOV公司不断对液压大钳进行改进,以满足日益严苛的钻井作业的需求和扭矩要求)所示。
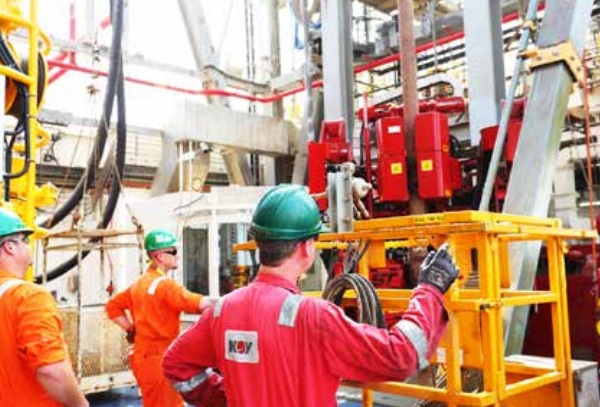
图1
然而,这种转变也给钻井承包商带来了新的挑战。扭矩要求的增加会导致接单根、接钻具、卸单根、卸钻具上扣和卸扣效率下降,还可能会导致NPT(非生产时间)增加。此外,较大的钻具需要对钻机的井架和底座结构进行修正或加强,同时起钻时还会对钻杆接头和钻铤转接头本体造成磨损,导致潜在的问题出现。
在“Big Foot”推出约五十年后,NOV公司开发了新的液压大钳的标准。IRX-120的模块化设计结合了强度、精度和灵活性,可为现代钻井作业提供安全、可靠和高效的钻具处理。
为了适应当今陆上钻井作业的钻机需求,这款可配置的设备占地面积最小,由三部分装置组成。扭矩钳施加必要的正向力和切向力,提供接单根、接钻具上扣卸扣所需的扭矩大小。扭矩钳能对钻具施加高达135千牛米的上扣扭力,卸扣扭力可达163千牛米,还能对钻具提供三点接触以及60°的来回转动。
旋转钳运用旋转将需要连接的两根钻杆或钻具的一端连接到另一钻杆或钻具的一端,将公扣和母扣接在一起。市场上的IRX-120新型旋转钳,对于5
1/
2 in.的钻具、能给出6.78千牛米的最高扭矩。每次接单根或接钻具可节省3至5秒的时间。最终,装有轨道的操作装置将整个钻具精准一致地摆放在钻台上预定的位置。
此外,IRX-120型旋转钳随时可以自动化操作;还可进行远程操控,并能与钻机的控制系统集成于一体,见图2(IRX-120型液压大钳的模块化设计和最小占地面积的理念为现代钻井作业提供了安全、可靠和高效的钻具处理。这款液压大钳随时可进行自动化操作,使其能在自动化钻井作业中进行操控和监控)。此功能使该款液压大钳成为自动化钻井进程的一部分来进行操控和监控,从而能使钻井工人避开钻台上的危险区域。
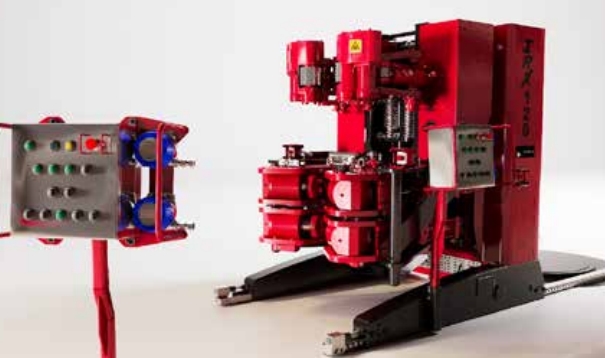
图2
自动控制不仅能通过降低人员伤害或人为错误的风险来提高安全性,而且还能确保接单根、卸单根操作的可靠性和可重复性。液压大钳还被设计用于捕获输入给钻机控制系统的操作数据,这些数据可用来优化接单根作业的操作过程、性能指标跟踪,最终能使钻井队实现预测性维护。这种数据驱动的方法进一步提高了作业效率和可靠性,同时还能减少昂贵的 NPT。
NOV公司正在采用ATOM RTX创建一个非人工钻台,ATOM™ RTX 是一个先进的、全自动化的机器人系统,可执行各种任务,以提高钻机性能,如图3(NOV的机器人系统 ATOM RTX 可自动执行重复性作业,让钻井工人远离易受到伤害的危险区域)所示。这个机器人系统自动执行重复性任务,让钻井工人远离危险区域,从而提高钻井作业的整体安全。
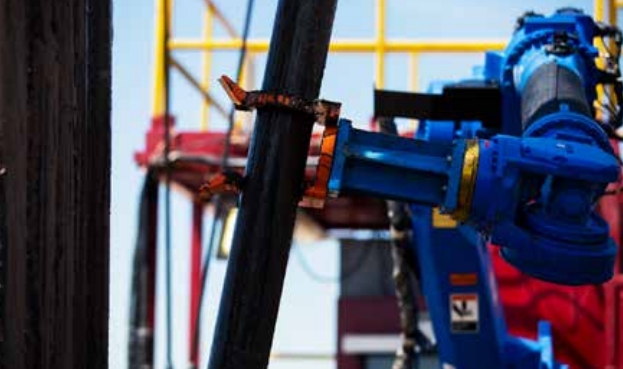
图3
该系统的可靠性和可预测性的操作性能可显著提高作业效率。ATOM RTX及其可互换的末端执行系统能够以高精度和可重复的操作特性执行各种任务,例如:对扣时可导向对准、摆尾、自动立柱摆放、可以高精度和可重复的动作抑制泥浆泄露,如图4(ATOM RTX可靠且可预测的性能有助于实现钻井效果的一致性)所示。这也消除了与人工操作相关的可变性,无论疲劳、天气或经验如何,ATOM RTX都能应变自如,从而减少了代价高昂的作业延误和停工时间,实现了更可靠和更一致的钻井效果。
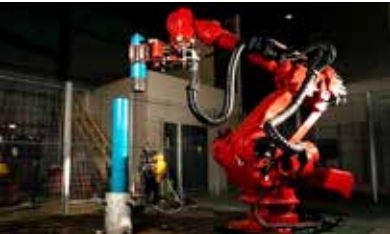
图4
该系统的模块化和可扩展的性能使钻井承包商能够根据他们特定的需求和现有设备来定制技术,优化潜能以应对钻井作业的独特挑战,无论是陆上应用还是海上应用。在加拿大的首次陆上商业运用中,ATOM RTX执行了一致的手动任务,实现了NPT零的操作和无形的时间损失。
未来的钻机
NOV积极主动的钻井自动化方法使公司能够开发满足当今和未来要求的集成技术和产品。随着该行业不断面临的成本压力、技能短缺和对更可持续实践的需求等挑战,自动化和机器人技术的日益普及对于推动创新和保持竞争力至关重要。
将自动化和机器人技术集成到钻井过程中不仅仅是提高运营效率的问题,也是保护钻井平台工作人员福祉的问题,以及最大限度地减少行业对环境影响的关键一步。随着该行业不断突破建井周期的极限天数,对更先进、更可靠的钻井技术的需求只会变得更加迫切。
通过利用工业机器人和先进的控制系统,NOV公司开发了如IRX-120液压大钳这样的工具产品,该产品可更轻松地改装到现有的钻机上,无需对钻机进行重大修改。这种方法使钻井承包商能够利用其现有的设备,将其转变为未来的钻机,从而提高钻井作业的安全性、可靠性、高效性和生产力。
结论
实现全自动钻井作业的努力已经进行了数十年的实践,还将在这个不断变化的行业中继续尝试下去。尽管如此,通过将自动化和机器人技术集成到钻井工艺中,该行业已经在提高安全性和效率方面取得了重大进展。
随着该行业面临越来越多的挑战,采用这些尖端技术对于推动创新、保持竞争力和确保该行业长期生存下去至关重要。NOV公司专注于开发易于集成到现有钻机和现代化工艺流程中的自动化技术和机器人解决方案,这证明了该公司致力于支持钻井承包商向未来钻机过渡的承诺。
钻井自动化的好处不仅仅局限于安全和效率。通过让钻井工人从危险区域和易伤害区域的作业环境中脱离,重新定位专业知识,最大限度地降低人为错误导致的风险,这些技术还可以促进更可靠和更可预测的钻井效果。反过来讲,这也能改进施工决策、更好地分配各类资源,提高整体钻井绩效。