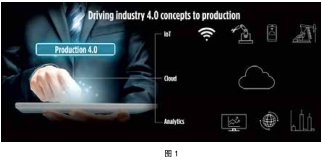
油价暴跌摧毁了能源市场,许多石油公司或运营商的资产流动性被削弱,流动资金锐减,这让以往可行的项目面临关闭的困境。利润的梦想遭到了搁置,因为项目经理们都在争相寻找各种方法,让他们的冒险和投机行为保持在黑暗中。当然,这其中的主要挑战是以更少的资金和更少的员工做更多的事情。
随着该行业锁定资本支出,利益相关者必须充分利用他们的资源才能保持企业的活力。然而,由于运营商们迫于更精明和更快的工作,该答案就是技术。行业发现它正处于生产绩效新阈值的尖端。
答案就是技术。但不是任何代价的技术。虽然石油天然气行业拥有诸多快速而广泛的接受技术的例子——想想过去十年非常规钻完井技术的突破——该行业为采用新的创新技术仍在顽强而缓慢地抗争。
如果曾经有一段时间可以超越对投资的恐惧,那么这个时间段就是现在。如果说曾经有一段时间可以接受突破性技术的话,那么这个时间段也是现在。拥抱工业4.0的潜在能力和数字化技术不再是一个简单的效率问题,它是在经济低迷甚至衰退时期能否保持经济活力和生存下去的答案。这是我们作为一个行业能够获得盈利的唯一途径,这将对今天和未来产生重要影响。
数字化为投资回报带来了确定性
利用工业4.0的潜在能力,如今通过整合开放式体系架构,几乎任何人都能访问以往无法想象的效率和控制的阈值。工业4.0包括物联网、云计算、边缘连通性和先进的数据分析。物联网由数字连接的物理设备组成,通过经验数据和远程控制提供系统支持和运作效率。
云计算允许这些设备通过互联网托管的服务器实现网络连接,这些服务器存取和管理数据,同时也减少了基础设施和复杂性。然后,边缘计算提升了智能设备的连通性,智能设备可根据动态数据和历史模型做出实时、自主的决策。
作为一家领先的井筒生产解决方案的企业,威德福公司设立了一门在许多行业(如制造、物流和娱乐)得到验证的采用工业4.0概念的课程,并将其运用于生产阶段。拥抱数字化不再是一个简单的效率问题,它是在经济低迷甚至衰退时期保持经济活力和生存下去的答案。威德福称之为生产的4.0阶段。它代表着近乎完美的资产效率,具有超快速的回报和丰厚的长期利润。
生产4.0解决方案对运营商投资的快速回报给予一种溢价形式,随后是随着时间推移的显著值,见图1(生产4.0解决方案通过优化从井下到销售点的资产设施的生产率,可立刻形成更多的现金流)。在平均仅有三个月的时间,运营商们正在收回他们的投资,同时还将增加数百万的增量收益,即使在当前的市场低迷时期也能实现。
这些收益的基石是ForeSite生产优化平台。这个软件平台利用设备每个角落的数据来共同提高一个储层、相关油井和地表设施的绩效水平。这个独特的单一平台集成了基于物理学模型和先进的数据分析,以增加设备的正常运行时间,并最终延长设备的使用寿命,见图2(ForeSite生态系统利用物理学模型来提高生产力、降低成本和提高员工工作效率)。这个安全且易于维护的平台为整个生产创建了一个生态系统,使石油公司拥有实现其最大化产量和降低运营成本的前瞻性手段。
利用ForeSite生产优化的优势,威德福公司现在提出了一种无资本支出的方法,通过使用这种方法,投资者可以立刻形成更多的现金流,优化其设备的生产力和减少总的支出,见图1。此外,经过验证该平台已具有降低设备故障率和严重度的功效,这将使现场工作人员需求减少,从而节省更多成本。就中期目标来看,这些战略通过数字化方案保持和提升企业资产的价值,方法是建立基准数据集,实现精准操作,使精准控制关键业绩指标向前发展。反过来,这些数据还能快速实现人们渴望的收益,增加现金流、平滑生产曲线、以及减少失误或失败。
即时投资收益率
范例一,哥伦比亚石油公司在几个月内将产量提高了6%,因疫情导致的封锁期间,井的重新启用率增加了36%。生产4.0解决方案提升了即时运营价值。在ForeSite第一阶段推出后的几周内,管理着近3000口油井的一家大的哥伦比亚石油公司提高了产量和效益。第一阶段实施覆盖了600多口井,这些井被确定为一个积极生产的电潜泵采油的子集,以供进一步分析。使用ForeSite平台的油井趋势布局,对每口井的生产历史和运行状况进行分析,以确定增产潜力。
这一发现过程提出了对几口井的增产策略进行细微修改的一些建议,这将促进增产,而无需额外资本支出。然后,该运营商选择了这些井中的一口作为样本井来测试举升策略,并修改了每口井的电潜泵电机的频率,以匹配ForeSite软件提出的建议。在实施这一举升策略后的头几周,该运营商取得了一项经认证的6%的产量增长,还预测了额外的收益。对举升策略的这些修改使年收益额外增加了325万美元。
ForeSite平台使该运营商能够推出他们企业范围的数字化战略。威德福公司提供平台安装、技术支持及应用培训的全程服务,包括各种增产方式、地面设施及输油管道的优化服务。随着工作的继续,据报道,未经认证的额外增产达8%,预计这些设备总的增产建议将使该运营商获得更高的产量。
随着哥伦比亚进入一年一度春季到来的雨季,该国石油公司的即时节约和收益仍在继续。在ForeSite平台安装后,这家常规油藏的运营商在新冠病毒全球封城期间经历了电力断供。多日大雨造成的洪水导致了轮番停电,影响了其中的三个油田,其中包括1000多口采用电潜泵举升采油的井。经历了三天的降雨,该石油公司面临近850口电潜泵采油的井失去电力供给,每天的石油产量损失高达14500桶。
ForeSite平台让控制室的操作人员能在不到一分钟内就识别出断电事件。恢复供电后,一位操作员利用ForeSite发出一条远程重启指令,该指令恢复所有油井正常工作的速度比以前快了36%。依从新冠病毒的规则,立刻重启油井的过程仅耽搁了3分钟的停机时间。由于停电持续到第二天,一位操作人员在70秒内就恢复了28口油井的作业。之后,到了第三天,三个油田的近850口油井也恢复了作业。此外,ForeSite平台还能让每个控制室的操作人员识别故障,并在恢复供电时立即使用重启指令。三个控制室的操作人员仅用了56秒时间就使850口油井中的95%恢复了生产。
ForeSite平台能让操作人员最大限度地减少因多日轮番停电给油井生产造成的影响,以及以日产14500桶产油率累积带来的损失。ForeSite平台支持快速远程管理,而不是人工重启的做法,人工重启油井会造成巨大的产量损失和停机时间,按每桶原油40美元计算,这会导致高达170万美元的收入损失。再者,通过最大限度地减少停机时间和生产延误,采用ForeSite平台进行投资可让投资者即刻获得收益。
范例二,
二叠纪盆地的运营商创造出了1770万美元的年度增量收益。一家财富500强的生产商在美国及世界各地拥有着广泛的设备资产,成功地实施了ForeSite优化,推动了一项企业范围的生产优化方案。该方案的授权要求为多种方式的增产提供便利,包括自喷、抽油杆举升、气举、柱塞举升和电潜泵采油。数据无关的优化平台需具备整合多个系统的能力,包括第三方的软件系统,以及利用历史数据,同时整合来自现有物联网平台的实时数据源,以及其它现场分配和油井设计的软件系统。
ForeSite生产优化团队与该生产商合作,以评估4000多口井的生产战略和数据需求。双方团队共同商定了一个分阶段推出ForeSite平台的方案,该方案从80口井开始先导性试点,以建立关键业绩指标要求来管理整个企业采用的计划。ForeSite平台被安装在包括自喷、抽油杆举升、气举、柱塞举升和电潜泵采油的井上。该平台无缝隙地将所有数据管理和规划系统整合于一体,使操作人员能例外地管理这批试点井。
这种方法确定了许多增产机会,包括建议增加表现不佳的井的正常运行时间和产量。这次ForeSite平台的试点井超出了所有的关键业绩指标,而且立即得到了扩大,包括第一阶段期间推出的近1000口井,最终将在未来两年全企业范围内推广应用。
ForeSite平台支持所有增产方式的生产优化,同时还能提高员工工作效率以及增加设备的正常运行时间。全面推出后,该运营商预计每年至少可节省1770万美元。这些节省包括580万美元员工的效率提高、650万美元设备运行寿命的增加、以及使用ForeSite平台的这些井获得的额外540万美元的收益,这些井能够更快地从自喷采油过渡到人工举升采油。
ForeSite平台提供了监控业绩且具有识别所有储层、油井、地面设备以及管道设施改进机会的能力。这是通过将现有的数据系统与实时数据源、基于物理学的建模引擎、以及指令和控制功能整合到一个单一的生产优化平台中所实现的。试点井的成功促使了该运营商在整个企业范围内推广使用ForeSite平台。最重要的是,最初的快速通道投资让投资者能即刻获得收益而再为自己付费,这让该运营商能更积极地继续走向未来,为生产收益和成本节省带来更广阔的前景。
这些数字化方案和策略的亮点是它们为运营商们提供了即时的现金流和巨大的长期投资盈利的能力。作为一家生产解决方案的全球领导者,威德福公司的任务是降低所拥有设备资产的总成本(无论是30口还是30000口井),以及在全球范围内为各种规模的设备资产提供生产解决方案。这些策略已证明了自己是可靠的,并取得了令人惊讶的长期成果。
范例三,自主举升策略可提高产量25%,减少25%的回购气体。一家二叠纪盆地的运营商通过采用ForeSite Edge(一种具有自主能力的下一代控制器),完美地维持了最佳的井底液流压力。在采用这项技术之前,井上的设备依靠技术人员前往井场执行手动压力调整来控制采油生产。这种人工动手操作的过程通常需要一周八次单独前往现场进行操作,每口井这项费用的支出就超过了1000美元。
安装ForeSite Edge后,该运营商在渴望获得的井底液流压力的设定点上实现了100%的成功率,即使出现气体注入中断的问题时也不会有影响。该运营商可远程调控井底液流压力的范围,其范围由设备自主维护。总之,这种方法可显著提高员工工作效率,以及新冠病毒疫情期间操作安全的合规性。
采用ForeSite Edge技术,每口井平均增产了25%,其中的5%归因于自主控制技术。此外,持续优化通过减少25%的回购气体量,降低了运营支出。
范例四,边缘技术(Edge technology)为Power River盆地的石油公司减少了80%的井场巡查量。一家石油公司试图延长其容易发生故障的往复式抽油杆举升采油井的正常运行时间,这些采油井只能通过目视检查来发现故障。每口井都配备了一个变频器,而且处于高速运行状态。每次往复抽吸还容易出现间歇性的低泵填充。
威德福公司的生产优化团队为其在井场处理高频率数据和获取建模能力推荐使用ForeSite Edge控制器,控制器安装在每口井变频器的旁边,以增强油井的可见距离和数据的可用性。这些设备使工程师们能够远程监控关键参数和性能指标,包括:举升次数/每分钟、泵填充、有效运行时间、举升次数/每天、以及估算产量。这些数据和功率计记录卡有助于发现每口井的优化机会。
高频率数据和自动功率计记录卡模式匹配一旦到位,可帮助工程师们确定泵填充趋势,检测是否存有循环气体,这种循环气体可导致气体冲击、增加设备磨损、甚至使设备停止运转。利用系统推荐,该运营商使用ForeSite Edge远程管理功能更改变频器参数,将每分钟举升行程数减至最小、泵关闭行程数减至最小、以及每分钟举升行程缩减设置。这些参数的调整使产量平均提高了2%,井场巡查次数减少了80%,每年每口井设备的举升次数减少了50多万次,从而使设备的故障率降低了15%。
通过提出推荐的ForeSite Edge的变化值,故障减少了15%,折合每年1.5个泵损坏,每个泵损坏的成本为2.5万美元。远程管理功能提高了员工的工作效率,减少了现场巡查次数80%。ForeSite Edge还揭示了一些增产机会,这些机会就是产量增加了2%。基于初始安装的成功,该客户现在计划将ForeSite Edge解决方案推广应用于其它油井设备。
可观的长期收益
中东石油公司在三年内增加了1.56亿美元的收益。威德福公司的生产优化平台使中东石油公司能主动管控设备故障,实时发现新的增产机会,从而在一个三年期以及更长时间实现增产。该石油公司需要对1500多口采用电潜泵采油的井进行自动产量监测、分析和资产范围的优化,以及未来适应其它增产方式的选择。该方案还需要进行模式识别,以实现预测故障的管理,以及整合来自六个不同系统和数十个自定义模型的数据,其中90%具有潜在的数据质量问题。
作为有能力管理所有增产方式的唯一系统,威德福公司的方法建立并实现了这一生产优化平台。该生产优化平台使1500多口电潜泵采油的井实现了自动产量监测、分析与优化。这一方法可推广应用于更多的油井和各种方式的增产,从而能实时、主动地管控故障和把握增产机会。这种无资本支出的方法使原油日产增加了5000多桶,这意味着增产收入平均每年增加5200万美元,三年可增加1.53亿美元。
目前,油气行业最大的挑战就是用更少的资源做更多的工作。为了实现这一目标,运营商们现在大都关注短期收益。生产4.0解决方案通过优化设备资产的生产力,能让运营商立刻形成更多的现金流。通过减轻设备故障的数量和严重度,支出会即刻得到减少,现场巡查人员也能相应地减少。通过维持和提高设备资产的可用性,这些方法还能为企业的中长期发展提供更高价值。(文献作者:Manoj Nimbalkar,威德福公司。2020年11月发布在世界石油网站)