长期以来,尽可能快地进行钻井作业一直是衡量作业表现的关键指标之一。如果一个钻井承包商和一名作业方能够提前一小时甚至几分钟完成油井的钻探工作,那么这口油井就会被认为是成功的。然而,随着该行业所钻探油井的地质条件变得更加复杂,多区域开发和平台式钻井应用变得愈发普遍,并且在资金更为紧张的经济环境下生产时间安排也更加紧凑,井眼位置的精准度正成为衡量成功与否的一个同样重要的指标。数字化和自动化工具帮助该行业提高了钻井作业以及资产开发与管理其他领域的效率。
人工智能和数字技术提高了行业在最佳地质条件下精确定位井眼的能力,同时还减少了天数和深度特别是在油井定位精度方面,数字化资源正助力各公司缩小定向井井筒轨迹周围的不确定性范围,降低井筒碰撞风险,并使钻井人员和作业方能够避免井下出现代价高昂的错误。斯伦贝谢油井建设部门的数字化地下领域负责人丘克斯・阿克佩尼表示:“当我们谈到优化井筒时,我们说的是几个要素的融合:实时轨迹的精度、执行情况以及对油藏特征的了解。”他说:“当能够实现这些要素的技术相互整合时,我们就能兼收并蓄,两全其美。归根结底,这正是我们努力的方向。必须清楚地认识到,钻井、油藏评估、地质学和地球物理学等不同学科的技术正在融合。我们把这些技术整合在一起,以确保客户能最大程度地提升资产性能。”然而,即便该行业致力于降低井筒定位的不确定性,快速完井的需求依然存在。作业方仍在寻求缩短钻井时间,并在此过程中降低成本。
自动化和数字化技术有助于同时实现这两个目标——即使有时用于优化定位精度的系统会以牺牲机械钻速(ROP)为代价,但它们仍可通过减少非生产时间(NPT)和总井下作业天数,帮助作业方将井下作业时间降至最短。这些效率的提升能为每口油井节省大量成本。休斯敦石油公司产品管理总监托德・福克斯说:“归根结底,我们知道对客户来说最重要的是时间。时间就是金钱。缩短达到一定深度所需的天数,减少在井眼弯曲段花费的时间,并且能够将套管下至井底。所以,我们的客户非常清楚,不会一味追求瞬时机械钻速。他们追求的是使油井达到一定深度所需的天数最少。我们的很多合同都包含业绩考核要素,因此我们与客户紧密配合,使用能够帮助将达到一定深度所需天数减至最少的技术。”钻井人员和服务提供商都一致认为,在优化井筒方面,人仍将发挥重要作用,提供宝贵的见解。
自动化系统可以进行那些常常会导致人为失误的重复性计算和测量,但人们依然掌握着这样的经验知识:在特定地质条件下,底部钻具组合(BHA)可能会有怎样的表现,或者在遇到特定异常情况时该如何应对。将这些知识融入到自动化程度日益提高的井下环境中,将有助于钻出更精准的井筒。MS定向钻井公司的定向协调员亚历克斯·根森说:“每个系统都不一样,但如果你试图让任何事情实现自动化,就需要制定规则。要是你的规则不合理,那么系统就不知道该怎么做。自动化系统无法预测在500英尺外会出现什么情况。它还达不到那种具有直觉的程度。输入的是无用信息,输出的也必然是无用信息。定向钻井工人凭借经验能预见到某些事情可能会发生,即便从数据上看说不通,而且他们知道该采取怎样的行动。”
利用自动化整合不同学科领域
阿克佩尼先生将当前优化井筒定位所面临的挑战描述为实现“实时地融合轨迹精度、作业执行以及对油藏特征的理解”。在过去几年里,SLB一直专注于最大限度地发挥数字化和自动化能力,以帮助行业更好地了解特定油田的地质情况,并尽量减少在井筒定位方面对人工干预的需求,从而为作业方节省时间和成本。这些努力的核心是该公司在2022年推出的Neuro自主解决方案系列。该系列中的首个系统——自主定向钻井系统,运用了建立在地面和井下自动化工作流程中的人工智能算法,能够自行确定导向顺序。Neuro钻井自主解决方案由四个独立的子系统组成:一个地下情况分析顾问系统,它对地下数据进行解读,从而生成油藏的全面可视化图像;一个定向钻井顾问系统,它利用地下情况分析顾问系统的解读结果,为井筒推荐最佳轨迹;一个智能井下系统;以及一个地面咨询系统。在钻井过程中,这四个子系统相互结合,实现定向控制的自动化。
阿克佩尼先生说:“我们这样做是为了更好地了解地质结构。我们利用机器学习来进行模型训练,这意味着,当我们运用物理方法来识别不同的地质层时,我们的全局模型以及为特定油井所使用的局部模型,将帮助我们在解读过程中得出最高水平的准确度和精确度。这是一个让我们对油藏测绘和解读充满最大信心的系统,它有助于提高我们井筒定位的准确性。”在使用旋转导向系统(RSS)时,智能井下系统和地面咨询系统特别有用。传统上,使用旋转导向系统进行钻井需要人工操作,其中包括反复执行指令序列来控制井眼弯曲轨迹。这个指令序列通常包含定向钻井人员在地面进行的多次干预操作以及关于导向力、工具面方位和测量数据的下行链路传输。然后,工具数据会反馈到地面,以便对指令进行调整。阿克佩尼先生表示,这个过程,也被称为控制循环时间,可能需要几分钟才能完成。
通过在Neuro自主定向钻井系统中实现下行链路的自动化,这个过程可以瞬间完成。他说:“下行能力传输实际上就是信息传递。当你实现了它的自动化,信息会在需要的时候自行触发,而且系统知道何时需要在油井方向上对指令做出改变,以及改变到何种程度、持续多长时间。下行链路传输将车载计算机与井下工具连接起来,为我们在确定轨迹位置时提供了更高维度的精度。”自动下行能力的另一个好处是,它减少了钻井过程中所需的下行数量。例如,中东的一家运营商在2022年使用Neuro系统自动钻了一口井,井斜度为22°至90°,井身曲线段为2500英尺,水平段为5400英尺。Neuro系统最大限度地减少了满足所有主要目标所需的下行命令的数量。对于这口井,作业者钻了61/8-in。从测量深度9417到总深度14828英尺的水平段,平均每258英尺发送一个下行链路。与未使用该技术的邻井相比,下行链路之间的平均长度增加了36%。
此外,Neuro系统将井底下行所需时间减少了80%以上,使整口井的总时间仅为10分钟。去年,SLB在Neuro解决方案系列中增加了自主地质导向功能,这是一种闭环系统,能够实时整合和解读地下信息,以自动引导钻头穿过油藏的“最佳位置”,即油藏中产量最高的层位。在常规的地质导向作业中,地质学家手动解释地下数据以确定井目标,更新井计划和井眼轨迹,并将此计划传达给定向钻工。Neuro系统可以自行完成所有这些工作,有效地消除了人为干预地质导向的需要,减少了完成地质导向轨迹改变所需的时间。去年,在厄瓜多尔,SLB在ShayaEcuador的一口陆上井中部署了Neuro自主地质导向系统,钻出了2392英尺的水平段。在这次作业中,Neuro系统完成了25次自动地质导向轨迹变化,每次解释和决策周期平均耗时22秒。
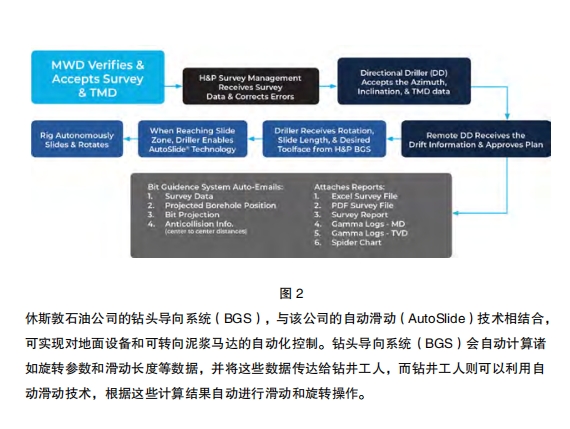
导向钻头
尽管在休斯敦石油公司优化井筒定位的工作中,自动化也占据着重要地位,但该公司认识到,人的主观判断同样不可忽视。福克斯先生指出,自动化系统仍无法完全取代钻井工人的直觉和洞察力。福克斯先生说:“归根结底,没有什么能替代经验丰富的人对某些关键点的判断,因为一旦我们判断失误,代价将极为高昂。在油井作业的不同阶段,不同的技术需要人工进行适度干预,而在某些阶段则需要更多的人为操作。我们仍然无法完全洞察井下的所有地质情况,而这种不确定性依然难以克服。”该公司的钻头导向系统(BGS)旨在在井筒作业中实现人工洞察力与机器洞察力之间的平衡。BGS是一种认知计算系统,能够针对传统的弯式马达定向钻具组合做出导向决策。福克斯先生说:“钻头导向系统是边缘计算与远程云计算的结合,以便做出最优决策。它会进行所有的数学运算,并分析每一种不同的井筒轨迹,从而得出结论:实际上,从各方面来看,某一种井筒轨迹是最合理的。一旦达到特定深度,它就会指示你进行滑动操作,让特定的工具面保持一定的英尺数。”该系统将随钻测量(MWD)供应商获取的定向测量数据录入电子数据记录仪(EDR),并生成一种数据传输流,可通过两种方式之一将其传送给钻机。一种方式是在井场部署一台计算机和通信设备,然后将其接入所需的WITS0数据传输流,并通过为休斯敦石油公司平板电脑设置的Wi-Fi网络显示输出结果。另一种选择是通过WITSML协议从电子数据记录器供应商处将数据传输至H&P远程指挥中心,信息在那里被输入到一个专用集线器中。
数据被传送到钻机后,会先进行分析,然后输出计算结果,这些结果会通过浏览器选项卡再传回电子数据记录器,并显示在仪表板上,同时给出后续的导向或旋转指令。随后,BGS内的人工智能和机器学习算法会计算出能以最短时间到达目标的井眼轨迹。BGS可与休斯敦石油公司的自动滑动软件配合使用,以实现对地面设备和可转向泥浆马达的自动化控制。不过,福克斯先生表示,即便有了这种自动化功能,BGS的设计初衷是作为对操作人员和定向服务供应商的辅助工具,而不是在整个过程中完全取代他们。一方面,操作人员可以选择不将自动滑动软件与BGS配合使用,这样一来,该系统更像是为手动操控底部钻具组合(BHA)的人员提供建议的工具。
该系统仍然需要油井计划、测量数据以及邻井数据——这些信息与定向服务供应商和操作人员在不使用该系统的情况下执行油井作业时所交换的信息相同。然而,即使操作人员选择使用自动滑动软件,休斯敦石油公司的工作人员和操作人员仍需选择各种参数并输入到BGS中,例如操作人员希望保持的距离或钻井窗口范围、最大狗腿度、测量频率、目标上方或滑动时的高低点,以及根据地质条件确定的任何“禁止滑动区域”。然后,休斯敦石油公司可以将多个目标输入到BGS中,并根据不断变化的钻井条件进行调整,自动滑动软件能够实时执行这些调整。福克斯先生表示,这种将人为因素纳入自动化流程的灵活性,对于应对钻井过程中出现的意外异常情况非常有价值。
“当遇到类似意外断层这样的情况时,邻井数据可能并未显示出它的存在。地质学家可能也没有意识到它的存在,但你却发现了这个意外断层,这可能就需要对油井计划进行调整。这个断层可能会意外地流出水来,从而引发一些问题。知道有经验丰富的人员在关注数据,并在需要时让你参与进来,共同研究解决方案,无论是调整油井计划还是继续向前钻探,这都是极其宝贵的。”事实证明,无论是否使用自动滑动软件,BGS在帮助作业方节省时间和成本以达到目标方面都非常有用。在伊格尔福特页岩区,有一位作业方在一个井场上使用了BGS,该井场上的八口油井彼此相距不到1英里,且几乎同时进行钻探,它们的岩性、井眼轨迹几何形状和BHA都几乎相同。并非该井场上的每口油井都使用了BGS。
该系统仅用于四口地质情况复杂且水平段较长的油井——未使用BGS的油井平均水平段长度为5300英尺,而使用BGS的油井水平段平均长度为6600英尺。与未使用BGS的油井相比,使用了BGS的油井在钻井时间、精度和弯曲度方面取得了明显更好的效果。使用BGS的油井在79%的时间内都能保持在油井计划轨迹5英尺范围内,而未使用BGS的油井这一比例仅为44%。此外,使用BGS的油井因随钻测量(MWD)设备或泥浆马达故障导致的非生产时间(NPT)为零,而未使用BGS的油井中,与MWD设备和泥浆马达相关的非生产时间占比达13%。这使得使用BGS的油井每口井的钻井时间总体节省了28小时,据休斯敦石油公司计算,这相当于每口井节省了约7万美元的成本。一家大型作业方还将BGS与自动滑动软件以及休斯顿公司的另一套系统——钻井扫描(DrillScan)软件配合使用,以帮助降低在海恩斯维尔页岩区钻探一口具有挑战性的油井时出现非计划起下钻的风险。特别是,该作业方对在井场上使用手动滑动方式钻完前两口油井后发现的高扭矩和高摩阻问题感到担忧。
DrillScan软件显示,前两口油井因井眼弯曲度高而导致摩擦系数大。基于这一信息,休斯敦石油公司的工作人员建议作业方将弯曲段的狗腿度从10°/100英尺降至8°/100英尺。在钻井过程中,BGS收集数据,以做出更高效的滑动决策,并通过自动滑动软件自动执行这些决策。与第一口和第二口油井相比,使用BGS/AutoSlide(自动滑动)/DrillScan软件组合钻出的第三口和第四口油井,平均井底钻井时间从196小时减少到139小时。据H&P计算,这57小时的节省相当于每口井减少了约14万美元的成本。虽然BGS最初是为弯式马达钻井应用开发的,并未针对旋转导向系统(RSS)工具进行配置,但福克斯先生表示,该公司已开始对远程RSS下行链路进行现场测试。他说:“这项新功能从本质上来说将减少钻井工人可能出现的错误。它让那些旋转导向系统(RSS)供应商能够充满信心地发送下行链路指令,因为他们知道这一过程无需人工干预。当他们将编码信息发送至工具时,指令会得到完美执行,而且无论他们身处世界何处,都能收到反馈确认信息。”
充分利用数字化工具
Patterson-UTI通过旗下的一家公司——SuperiorQC,简称SQC,在其自动化定向钻井控制应用程序中采用了一种基于云的故障检测、隔离和恢复(FDIR)系统。该系统运用机器学习算法来提供实时校正,从而最大限度地增加与目标生产层位的接触。SQC还提供HiFiNav测量管理系统,该系统可以估算旋转趋势和泥浆马达输出功率;以及HiFiGuidance钻头导向系统,该系统将这些估算值输入机器学习算法中,以计算出井筒的最佳形状和轨迹。HiFiNav系统会实时不断地调整其估算值,并将这些值传送给HiFiGuidance系统,从而能够针对给定的井段进行优化的超前预测和作业规划安排。对于使用这些系统的定向钻井工人来说,在执行油井计划以及使底部钻具组合(BHA)到达目标位置方面,自动化程度的提高带来了巨大的好处。Patterson-UTI的另一家子公司——MS定向钻井公司的根森先生表示,像SQC或其他数据聚合软件供应商所提供的这类能够对潜在碰撞风险发出警报的系统,在大型井场的钻井作业中尤其有价值。
根森先生说:“对于那些在一个井场上部署了多台钻机的大型作业方来说,会出现两台钻机紧邻着同时进行钻井作业的情况,我们希望这类软件能够实时向人们发出警报,告诉我们两口井的井眼轨迹正朝着彼此的方向延伸。它们之间相距多远呢?我们是否需要担心呢?”他提到了HiFiGuidance系统,该系统利用标准的随钻测量(MWD)测量数据,结合HiFiNav系统提供的实时旋转趋势和泥浆马达输出功率估算值,以15英尺为增量来计算井筒的形状和轨迹。根森先生说:“有些公司会在钻完一定井段后进行批量校正,有些公司可能会在每次测量后就进行校正,而不是在测量完10000英尺后才校正。这可能会产生影响,因为在那段井段长度内,井眼位置可能会发生很大变化——通常在25英尺到150英尺之间。使用SQC的系统,你只需将测量数据发送给他们,他们就会立即把校正后的测量数据反馈给你,不管结果如何。从我们的角度来看,这并不会耗费太多时间。我们把数据发给他们,他们很快就反馈回来了。”然而,他表示,尽管这些自动化系统是实现更精确井筒的关键驱动因素,但它们并非完美无缺。
例如,存在缺乏直观的用户界面(UI)的问题,用户界面就是钻井工人查看系统所处理的所有数据的屏幕。根森先生说:“这些界面只是数据聚合器。你能看到时间分配情况、底部钻具组合(BHA)的信息、性能报告,并且可以基于所有这些数据进行进一步分析。它只是把所有东西集中在一个地方。这减少了流程中的步骤,并且在某些情况下可能会有所帮助,比如有人没有发现问题,在没有相关信息的情况下就接受了目标更改。但从定向钻井的角度来看,严格来说并没有真正的人工智能。你输入自己认为可能会发生的情况的参数,然后基于这些参数得到相应的结果。”根森先生说,他希望看到自动化系统的用户界面在钻井过程中能实时纳入更多的历史数据。
这主要围绕着自动化系统作为终极数据处理器的基本功能。虽然这些系统能够解读数据,并就最佳轨迹向定向钻井工人提供建议,但实时提供历史背景信息,会减轻定向钻井工人在识别异常情况或发现井筒轨迹可能需要偏离系统生成的计划时,完全依赖自身过往经验的压力。“我希望看到更像是弹出式提示的东西,比如在这个深度,使用这种底部钻具组合(BHA)时我们是这么做的,或者我们当时看到了这样的机械钻速(ROP)。如果你知道自己要找什么,你可以去查找这些信息,但这会花费时间。我认为借助人工智能这些信息可以自动呈现。有些系统会利用历史数据为你提供钻井参数和预期机械钻速的指导,但通常情况下,那些数据是由软件供应商加载的数据文件,且只有已知的邻井数据集,一般不会包含在特定区域内所钻的每一口井的数据。”
P