钻井技术的不断进步改变了作业的面貌。今天,机器完成了许多几十年前靠人工完成的工作。持续的投资正在提供技术,将这些节省劳动力的设备转变为完整的自动化系统。
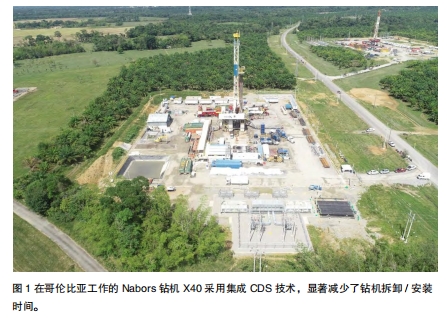
通过自动化实现价值
钻井承包商在复杂的作业环境中竞争项目。作业者想要高效、可靠的钻机,他们也希望与承包商合作,这些承包商不断应用技术来解决作业挑战,并提供可衡量的改进。与此同时,运营商正在寻找具有良好钻井性能和安全记录的公司,这些记录表明他们致力于降低风险和提高工人的安全。自动化使钻井承包商能够在每一层进行交付,如图1所示。当钻井活动实现自动化时,人们可以从重复性和潜在危险的活动中解脱出来,专注于需要在不同层次上思考的更高层次的任务。自动化减少了人为错误,确保了复杂钻井环境的一致性和可靠性。简化单个钻井过程的结果显示出可测量的性能改进。促使集成活动的概念,以实现更广泛的自动化,从而获得更大的收益。
下套管的更好方法
在常规的下套管过程中,提捞器采用升降机下放,携带管柱砝码,在猫道后将套管接头移至井中心,随套管接头在车厢内上移。在此过程中,司钻松开,将侧门升降机定位在滑轮中套管上方,然后关闭升降机,将链接上浮至井中心。工人用拖尾绳将管子拖尾,用手施加螺纹胶,然后将销钉定位到卡瓦中的套管箱内。将套管接头从猫道上吊装下来,并与残根中的现有接头对齐后,由船员进行连接,使用动力钳将套管接头与套管柱连接。然后,司钻人员拾取管柱重量,打开卡瓦,将套管柱下入孔内。这个过程在过去几十年的陆上作业中没有得到发展,它依靠船员在物理上组成套管柱。机械化是迈向自动化的第一步,因为它将任务从人力转移到机器上,利用发动机的动力来执行体力要求高的任务。机器以一致的精度和准确度持续地执行着劳动密集型的活动,执行过程比人类工作人员更加高效和安全。
机械化与安全
动力钳用于制造套管已有几十年的历史,它是工艺机械化的一个例子,改善了石油和天然气的操作。使用这种工具,更少的工人可以完成与只使用手工工具的更大的船员相同的工作量。动力钳增加了对扭矩施加的控制,使执行精确,过程可重复,同时减少了所需的人工搬运量。尽管动力钳在套管接头的上扣和脱扣方面有所改进,但由于需要人工干预,事故仍不断发生。许多工人都有过拉伤、扭伤和重复性应力损伤的经历(由于重复作业,如刺伤套管部分),以及在使用电动钳、升降机和其他设备时由于不注意而割伤、撕裂和夹住手指和手。这是推动变革的重要因素。提高机械化实现自动化——机器在最少人工干预的情况下执行任务、做出决策和控制过程——降低了受伤和事故的风险,并将性能提升到一个新的水平。这种方法使用集成解决方案,用我们的CDS(CRT)代替动力钳和升降机,体现了我们对任务的承诺,图2.
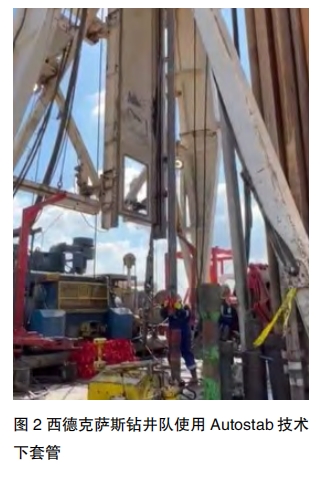
设计更好的解决方案
向自动化套管柱上扣组装的过渡始于对整个过程的回顾。通过评估确定了造成平井时间的常见因素,包括在接头中对齐套管下放工具(CRT)、弥补连接、以及套管柱的间歇性钻井液填充。该分析没有将重点放在孤立的改进上,如使用动力钳更容易地执行套管上扣和卸扣,而是将动力钳和其他机械化工艺的使用放在了管柱下放服务(TRS)的背景下,该服务将套管下入工具(CRT)集成到钻机及其钻机操作系统(ROS)中。显而易见,自动化CRT校准和上扣连接等关键任务可以解决常见的低效率问题,并消除许多与下套管相关的安全问题。完整的IntegraTMTRS解决方案包括机械升级和软件创新,以优化套管连接时间,并减少因人为失误而导致的接头损坏的可能性,这在历史上一直是安全事件的原因。
IntegraTM系统系统包括顶驱、套管驱动系统(CDS)和SmartROS®系统(图3)—后者是一种可实现自动化的专有智能ROS。顶驱为自动化CDS提供动力,使其能够旋转和往复移动套管柱至总深度,并利用技术来简化和自动化套管安装过程,遵循自动化工作流程/配方并实施最佳实践来给井下套管,同时保持最佳井筒完整性。这种整体方法消除了阻碍传统钻井作业效率和生产率的孤岛,并在自动化操作系统的控制下无缝连接多个流程。
理解螺母和螺栓
将CRT与钻机的液压系统相结合,将机器人流量转移到CDS工具。在机械方面,三个压力传感器提供反馈确认工具在提升管柱重量、释放管柱重量或在单根图3司钻利用SmartROS钻机操作系统从座椅上自动操作吊卡中处理套管接头之前是安全操作的。软件对顶驱动的逻辑进行了更改,使其能够适应套管运行的应用程序。将套管下入操作与钻机集成在一起的互锁和权限,消除了套管落入井内或单根吊卡过载的风险。该技术允许与钻机系统并行操作。钻井人机界面(HMI)——司钻用来与钻机交互的控制面板——在CDS与顶驱装配后,被置于两种可选的套管下入模式之一。这使得钻井HMI具有比CDS工具更全面的功能,并使司钻能够使用自动刺扎、自动填充和自动上料等自动化功能。这些自动化功能提供了对套管下入过程的控制,并以一致性的形式增加了价值,并且能够缩短每个连接的时间。在整个钻井过程中,这些加起来可以节省大量的生产套管作业时间。
在一次应用中,将CDS工具与接头对齐所需的时间从30秒减少到10秒。时间运动研究表明,使用基于软件的序列来自动化操作可以提供一致的性能和连接完整性,无论谁坐在司钻的椅子上,以弥合经验丰富的司钻和缺乏现场经验的司钻之间的技能水平差距。在西德克萨斯州的现场试验中,通过遵循基于软件的序列,CDS对比时间减少了67%。过去,CDS工具在接头中的校准过程取决于司钻,完井速度取决于司钻的经验水平,但随着自动化配方的出现,确保了整个套管下入作业的一致性,无需再进行经验丰富的猜测。配方管理器确保刺入距离始终相同,并且每次连接过程中施加的扭矩和速度不变。该系统还包括在装配任务开始时检测交叉线程活动的参数。
随着时间的推移,从将CDS工具与钻井平台的SmartROS®系统集成开始,编程工作不断得到改进。由于理论和基于现场数据的钻机物理控制之间存在差距,软件工程师正在输入代码,以达到历史上只有最有经验的钻井人员才能达到的精度操作设备。一个例子是改进块松弛时使用自动化妆。司钻通常会密切关注重量指示器,并调整松脱,使重量保持在规定范围内。最初的规范设计只关注于绞车松弛时的每英寸螺纹数。经过多次试验收集操作反馈后,工程师们修改了代码,将重点放在重量上,这使得保持更严格的重量窗口。
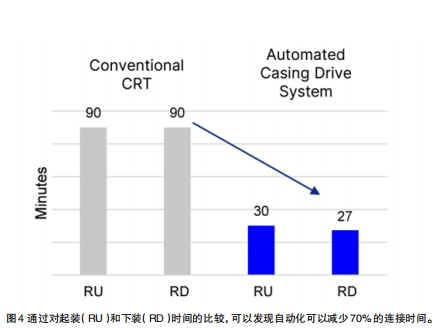
在现场证明价值
在钻井自动化的一个应用中,哥伦比亚的一名操作员采用传统的下套管操作,需要将几件设备移动到钻台,这需要额外的工作人员,并使更多的人员暴露在红区的安全风险中。作业者将常规套管下入改为IntegraTMTRS集成套管下入,安装自动CDS,并将其液压连接到顶驱,从而降低了作业人员的风险。使用HMI屏幕,司钻能够监督操作,因为系统遵循输入的参数,以确保在整个套管下入图4通过对起装(RU)和下装(RD)时间的比较,可以发现自动化可以减少70%的连接时间。过程中连接一致。消除了估计每个连接所需的手动扭矩应用的猜测,并使工作人员远离红色区域。自动化缩短了每次连接的时间,将套管性能速度提高了21%,将起下钻时间缩短了70%,相当于4小时(图4)。自动对扣是套管柱上扣过程的关键部分。为了启用Autostab,配方管理器存储并应用OEM推荐的参数,包括旋转和扭矩的顶驱设定值,以及为连接构建过程中每个环节指定的速度输入。值得注意的是,在旋转增加到更高的自旋转/分钟(RPM)之前,交叉螺纹转/分钟被设置为低,以检测初始旋转中的交叉线程。在组装关节的最后一转中,肩部向上的转速被调整到较低的速度,并施加最佳扭矩。在顶驱控制CDS的30~40秒内,钻井工人可以离开红色区域。自动化系统还消除了钻井液充填套管柱时的间歇性停顿。配方管理器中的自动填充功能允许司钻输入每个接头的计算冲程来控制泥浆泵,在套管连接完成时通过CDS进行通信。
在一根500接头的生产管柱上,传统的每20接头加注套管10分钟,共加注25次,总计250分钟。(略多于4小时)。另一个有助于缩短平井时间的因素是将CDS工具与已装入转盘套管柱中的接头对齐。在人工作业中,该过程所需的时间取决于司钻的专业知识。在装置中增加了一个连杆倾斜稳定器,以减轻外部因素,如阵风会影响连杆倾斜并影响对齐,并在执行器上放置了一个支架,并固定在每个连杆倾斜上,以限制运动范围。自动化妆微调,以减少步骤之间的过渡时间,加快进程。这些阶段组合成一个完整的上扣序列,由司钻按下按钮激活。如果连接不正确,联锁装置会冻结作业,阻止司钻继续作业,直到警告得到确认和解决。这一特点大大降低了套管柱落入井筒的可能性。Autostab专有技术首次应用于二叠系盆地7.625英寸中间套管上。连接顺序的自动化为司钻减少了四个步骤。现场结果显示,与传统安装工艺的2:06分钟相比,Autostab的卡瓦连接时间为2分12秒。虽然Autostab技术的首次试验反映了手动和自动上扣之间的连接时间差异可以忽略不计,但它证明了该技术实现一致性的能力,弥合了现场有经验和无经验的司钻之间的差距。时间/运动对比显示,当使用自动化软件时,从插入CDS到完成连接所需的时间更短,如图5所示。
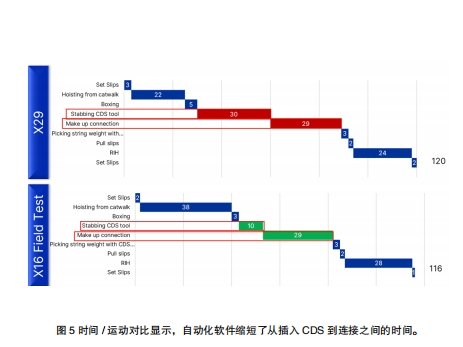
自动化的未来
自动化下套管有助于弥补经验不足和经验丰富的钻井人员之间的差距,并简化整个过程,以提高一致性和效率。集成远程扭矩转向、液压升降机和猫道尾臂,正在彻底改变钻井,同时减轻潜在的风险。尚未开发的能力有望在短期内实现更大的自动化。海上钻井的自动化已经成为可能,TRS提供了一套全面的服务和技术,可以安全有效地下入套管和油管,允许一个操作人员控制多个设备。工程师们正在研究改进陆上自动化程度,评估从猫道到油井中心的尾管过程自动化概念,以提供完全免提的套管下入,使作业者能够规定套管下入的深度和速度,规定填充每个接头的泥浆量,并监测位移,因此司钻只需监督处理过程。如今,将系统与SmartROS®技术结合在一起,可以在全球陆上钻井平台上扩展自动化。智能钻机操作系统支持的基于深度的配方具有扩展自动化的潜力,可以根据深度和下入井速设置深度触发器来制定套管配方。很明显,该行业将继续追求自动化和优化,以获取越来越大的价值。采用自动化等技术进步可以提高作业效率,并为参与钻井作业的每个人创造更安全的工作环境。