油气钻探钻头的发展趋势
时间:2024-10-28 16:34
来源:2024石油与装备10月刊
作者:小编
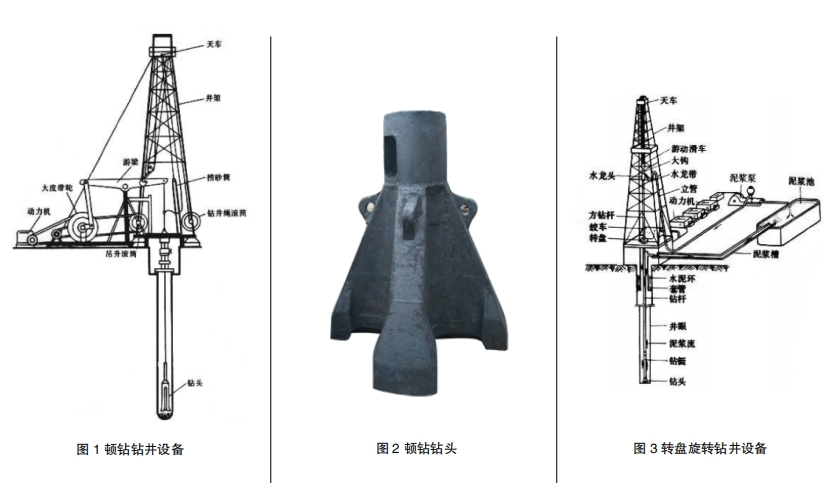
四季交替、大地轮回,春种秋收,这是大自然的规律;同样,钻头也在轮回,从最初的冲击性顿钻钻头,到旋转刮切的刮刀钻头,再到旋转冲击的牙轮钻头,钻头的复杂度达到最高,然后接替的是结构较简单的PDC钻头,一种进化了的刮刀钻头(旋转刮切型钻头),按照这种发展脉络,接替PDC钻头的应该是进化了的冲击型钻头,一种旋转刮切冲击型钻头。钻头结构趋于简单而功能趋于复杂。
传统钻头
钻头的轮回是人们对钻进效率不断追求的结果,同时也是钻头钻凿对象及环境变化的结果。早期人们在开采浅的低压油、气井时采用顿钻的钻井方式(图1),钻头是结构简单的钢制冲击型钻头(图2),用钢丝绳把顿钻钻头送到井底,由动力机驱动游梁机构,使游梁一端带动钢丝绳和钻头产生上下冲击作用,破碎岩石。公元前八世纪我国在冶铁业的发展中形成了顿钻钻井技术,19世纪中叶西方国家用蒸汽机做动力,对顿钻钻井技术进行了改进,并用于油气钻探中。
顿钻钻井适用于较软的地表钻探,机械钻速慢,不能满足加深钻井的需求,于是,20世纪初,人们将1863年法国土木工程师RudolfLeschot发明的旋转钻井技术应用于油气钻探。旋转钻井是用钢制钻柱将钻头送入井底,在地面驱动钻柱旋转,同时控制钻头上的重力(WeightonBit,WOB)使钻头钻入地层并破碎岩石。目前,这种钻井方式仍然在用,并从转盘旋转(图3)升级到顶驱旋转(图4)。刮刀钻头是旋转钻井使用最早的一种钻头,从二十世纪初开始采用旋转钻井进行油气钻探时就开始使用这种钻头。钻头体用中碳钢材料制成,下端焊接刮刀片和分水帽,上端车有螺纹与钻柱连接。
牙轮钻头
刮刀钻头是一种切削型钻头(图5),其切削岩石的过程类似于刀具切削软金属,刀片在钻压的作用下吃入地层,与此同时刀刃前面的岩石在旋转扭矩的作用下不断产生塑性流动,井底岩石被层层剥起。刮刀钻头结构简单,制造方便,成本低廉,用于钻进可钻性4级的泥岩和页岩等软地层,但在硬研磨性地层钻进,刀片难以吃入,钻头磨损快,机械钻速低,有时还出现憋跳现象,对钻具和设备寿命有一定的影响。随着石油开采深度的进一步加深,地层硬度增大,地面设备无法为刮刀钻头提供足够的破岩扭矩,于是扭矩小、破岩效率高的滚动式旋转冲击破岩的牙轮钻头(图6)问世,在很长一段时间内成为石油钻探的主要破岩工具。
1905年出现第一只牙轮钻头,随后的100年里牙轮钻头技术不断进步,从两牙轮钻头到三牙轮钻头,从滚动非密封铣齿牙轮钻头到滑动密封镶齿牙轮钻头,使得牙轮钻头能够使用于几乎所有地层的钻进。常用的三牙轮钻头主要由钻头体和牙轮组成,其中钻头体由三片牙掌组焊而成,牙掌下端凸出的轴颈上安装牙轮,牙轮外锥车成不同锥角的锥台,形成齿圈和齿槽,齿圈或铣成齿状(铣齿钻头)或钻孔镶入硬质合金齿(镶齿钻头)。牙轮钻头工作时,牙轮一方面随钻头体旋转(公转),另一方面绕轴颈旋转(自转)。钻头牙齿在钻压作用下吃入岩石,同时对岩石产生旋转冲击或滑移剪切作用,使岩石破碎形成岩屑。由于牙轮钻头的滑移剪切作用较弱,因此,主要属于一种旋转冲击型钻头。尽管牙轮钻头的使用具有广谱性,但存在使用寿命短、钻头进尺少的缺点,尤其是存在牙轮脱落的风险,使得人们不断寻找新技术来替代它。
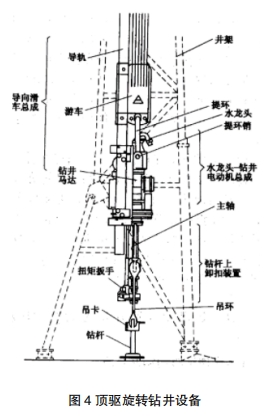
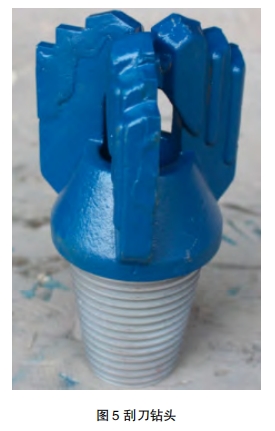
PDC钻头
1971年,美国通用电气公司发明了PDC钻头即聚晶金刚石复合片钻头,首次应用于1973年,但由于金刚石复合片性能差,设计技术不成熟,在早期约15年时间内PDC钻头发展缓慢,到1988年其在世界油气钻井市场总进尺所占比例仅为5%。PDC钻头本质上属于旋转刮切式钻头,以切削方式破碎岩石。上世纪90年代,定向井、水平井技术发展起来,改变了之前以垂直井为主要井型的模式,单井长度显著增加,而且深井也逐渐增多,寿命较低的牙轮钻头越来越不适应了,而随着技术的进步,高耐磨人造金刚石加持的PDC钻头结合弯壳体螺杆钻具(图7)的使用效果凸显出来,其机械钻速、单趟进尺都远远高于牙轮钻头,而且没有牙轮钻头掉牙轮的风险,于是很快就完成了对牙轮钻头的替代。从以上油气钻探钻头的迭代过程来看,冲击和剪切是破碎岩石最有效的方式。单一的冲击型钻头,包括完全冲击型的顿钻钻头和以冲击为主的牙轮钻头,单一的剪切型钻头,包括合金刮刀钻头和PDC钻头,在其规模应用阶段都取得了不错的使用效果,但需求总是不断在提高,技术也不断在进步,近年,冲击和剪切复合型钻头或钻头工具组合便陆续推出。
贝克休斯公司2011年推出的牙轮和PDC混合钻头(图8)就是一种冲击和剪切复合型钻头,其将牙轮的旋转冲击作用与金刚石复合片的剪切作用结合起来,在软硬交错、夹层等不均质地层使用,取得了非常好的效果。而近年国内推出了复合冲击器(图9),在钻进过程中给钻头施加一定频率的轴向冲击和扭转冲击,结合高抗冲PDC钻头,在硬研磨性地层也取得一定成效。
目前,中国页岩油气、致密油气开采方兴未艾,深井、超深井,井深直指万米,钻头面对的是“开次一趟钻”的进尺目标、不断提高机械钻速的需求以及高温、高压和特性差异较大的多套地层的钻井环境,螺杆钻具+PDC钻头组合由于其耐温性受限,旋转切削难以高效破碎极硬地层、硬研磨性地层和冲击性地层等因素已无法胜任,人工智能加持的电动钻具+剪切冲击复合型钻头将是油气钻探钻头钻具组合的发展趋势。通过混合钻头和复合冲击器的应用,已证明剪切冲击复合型钻头较单一的冲击型或剪切型钻头机械钻速高,但混合钻头仍存在牙轮寿命低的问题,复合冲击器的可控性也非常不足,高抗冲、抗磨的PDC钻头还需要进一步提升性能。最近,人工智能技术爆发式发展,给油气钻探技术的迭代提供了新的途径,通过电动钻具提升井底钻头钻具组合的可控性,人工智能模型+钻头前侧及周边岩石特性超前探测提升钻进的智能性,由此必将使油气钻探技术得到跨越式发展。
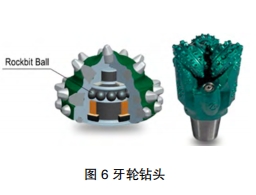
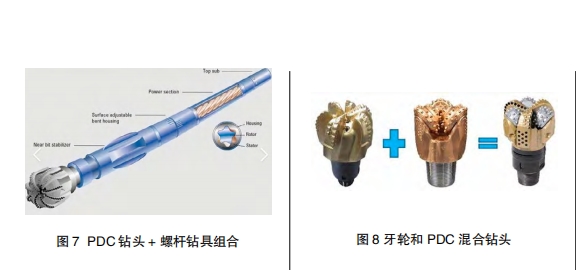