一种新的、高密度数字测井技术点亮了井眼中的高扭曲度区域,改善了生产设备的井下安置,减少了设备的损坏率。数字技术提供的高密度井眼扭曲测井,解决了钻井和油气开采作业的诸多问题。一个未讨论的领域,即高密度井眼扭曲测井是如何帮助确定人工举升设备最佳的井下安置,延长一口井的寿命。
在过去,测井方案并未涉及井眼扭曲测井,而是依靠随钻测量(MWD)进行井下勘测或者采用带测径器的间歇陀螺仪进行测量,分析基于狗腿度(DLS)的井眼几何形状。这种测量,对于特定的应用虽然其测量质量通常是可以接受的,但并不提供高精度、高分辨率井眼扭曲度和遇阻分析。为了解决市场设备的这一缺陷,Gyrodata服务公司开发了一种新的拥有专利权的高密度井眼测井技术,称作MicroGuide。从这一新技术给人的印象来看,在如何处理现代油田中套管井的测井方面呈现出了一个步骤的变化。
理论
在规划如何钻一口井时,井眼的预定轨迹通常被认为是一条相对平滑的曲线。偏离这一轨迹一般被称作井眼扭曲,井眼扭曲又可以井眼扭曲度来衡量,井眼扭曲度是通过取两点之间实际距离的比率来确定的,包括任何曲线或弧线,将其除以直线距离。当井眼轨迹在较短的距离内发生较大的变化时,会出现各种问题,包括穿过轨迹偏离段的套管设定和下入,以及穿过同一井段安装和通过采油设备。之前和目前的系统都在很大程度上探索使用测量井眼的狗腿来提供有关井眼轨迹的信息,但这些信息往往很难利用,因为其缺乏真正优化井眼定位所需的细节和清晰度。
MicroGuide系统在井下运行,接收来自井眼测井记录多个测量点的数据。数据采自陀螺仪工具、磁性仪器,或其组合。此外,该系统根据接收到的数据,为井眼轨迹定义参考线,确定井眼轨迹与参考线的位移。通过基于这一输入信息的一系列计算,能以三维(3D)形式可视化井眼形状,因为这一物理系统被下入井下、在井下运行、发送数据到地面。将这一信息输入进计算机并呈现出来,可让石油公司就油气井的开发做出关键决策,更有效地钻一个低扭曲度且与计划轨迹一致的井眼。在钻完该井段后运行MicroGuide系统的情况下,了解和掌握井眼扭曲度能帮助石油公司就人工举升和其它设备的井下安置做出更好的决策,将井下设备安置在低扭曲度区域。否则,如果没有利用该系统获得细节和精度更高的数据,就不可能做出这种预先知情的决策。
应用
改善电潜泵ESP的位置安放,提高产量,消除设备损坏。中东一家石油公司在钻完一个侧钻井眼后,之前曾在5800ft(ft英尺,1ft=0.3048m)的测量深度安置了一台电潜泵。虽然电潜泵最初的产量徘徊在日产原油390桶左右,但此后不久下降至0桶/日。在开始修井作业之前,需要进一步调查,确定井眼状况,因为该公司怀疑产量不良的原因是电潜泵潜入或安置的深度不足。电潜泵最初安放选在了一个浅的位置(约在5700至5900ft测量深度之间),因为7in尾管处于井眼较深的高DLS(5°至7°/100ft)井段,如常规MWD测量所示。
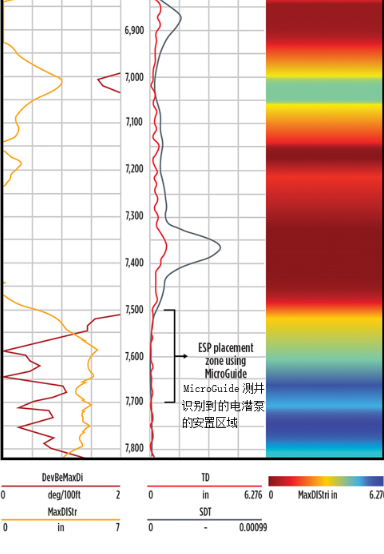
图1
Gyrodata服务公司评估了现有的井下数据,以确定合适的行动路线。根据现有的信息,实施了MicroGuide高密度井眼扭曲测井服务,对井眼进行评估,给出一个更准确的电潜泵的安放位置。向该石油公司提供了扭曲度、最大工具外径,以及其它与之有关的分析结论,这些信息通常不是通过传统MWD工具的DLS计算获得的。MicroGuide技术表明,穿越6000至7500ft的高扭曲区域,将电潜泵安置在7570和7770ft之间是可能的,这是产量高产出的首选深度。见图1(图1:利用常规MWD技术,该石油公司认为最佳的电潜泵安置位置在5700ft和5900ft测量深度之间,然而,高密度井眼扭曲测井发现了另一个低DLS区域,在这个区域安置电潜泵会获得更高的产量,故障也会较少)。在进行了新的位置确定后,这家石油公司继续使用该技术,以确保安全操作,避免在向井下输送过程中对电潜泵造成任何损伤。
在7650ft的位置成功安装了电潜泵后,根据测井数据,电潜泵再次开始生产,产量从390增至600桶/日。除了几乎54%的产量增长外,该石油公司还通过避免每3至4周电潜泵的启/停作业,包括中途修井,实现了时间和成本的节约。通过揭示传统MWD定位的局限性,MicroGuide测井服务成为了石油公司未来油气井设计规划的部分内容,使他们能在井下正确的放置电潜泵,避免出现意外过早的损坏。
在拉丁美洲,一家石油公司正面临电潜泵故障的挑战,因时间损失和设备损坏而遭遇重大成本损失。在遭遇了困难的下套管作业后,该石油公司怀疑井底钻具组合(BHA)存在问题,但井已按计划进行了钻井,而且,依据的是MWD传感器采集的数据实施的定向钻井。为了找出设备损坏和故障的原因,该石油公司决定在井的9⅝-in.套管段下入MicroGuide系统实施高密度测井。
最初钻这口井采用了旋转导向系统(RSS),井下采用了一套降陀螺 + MWD工具进行测量,下至2705m(8875ft)。MWD测量只收集数据至总井深3272m(10750ft)。MWD最后测量的400m(1312ft)数据表明,就方位角而言,这部分井段从58°倾斜至70°。然而,有迹象表明,12¼-in. BHA在起出井眼过程中出现了一些问题,从3290至2775m (10794至9104ft)进行了倒划眼作业,从3290至3156m(10794至10354ft)进行了必要的井眼清理。在下9⅝-in.套管时,管柱在3264m(10709ft)处遇卡,且无法继续下入。重新尝试上提管柱无效,油公司必须执行一次清理作业,将套管遇卡区域清理干净。在下入完井设备并将电潜泵安置就位后,油气生产可以短暂地进行,直到电潜泵出现故障为止。
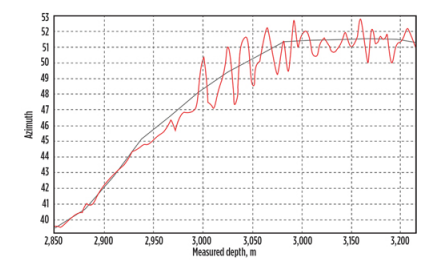
图2
运行MicroGuide系统能让石油公司以1ft的间隔跟踪井眼轨迹,这表明,相比石油公司以前仅凭MWD数据看到的结果与井是如何钻进的真实结果有着截然不同的情景。见图2(图2:灰色线显示了最初的井眼轨迹,采用了每个点采集的测量数据。根据从MicroGuide系统获得的测井数据,红色线表示真实的井眼轨迹。套管柱的严重扭曲和微狗腿造成了设备的损坏,电潜泵未安置在最佳的位置)。虽然检查MWD传感器数据未见到有严重误差的证据,但这口井未曾像预期的那样按正确轨迹钻井,而是根据陀螺仪测量的数据决定钻进的。该石油公司已因时间损失和设备损坏支付了超过700万美元的费用,而MicroGuide系统在套管内识别出的微狗腿并未被MWD测量系统所检测到,同时,MicroGuide系统还采集了微狗腿长度间隔点的数据。高密度井眼数据揭示了现有BHA的性能缺陷,它帮助石油公司确定电潜泵的最佳安放地点为井眼向上150m(492ft)的位置,避免了电潜泵的进一步损坏。
检测到井眼异常后优化抽油杆引导器的安放位置。一家石油公司在美国德克萨斯州接近加拿大的阿纳达科盆地为一口井配备了一个有杆泵人工举升系统来提高产量。仅仅一周后,该系统就崩溃了。该公司发现抽油杆存有大范围损坏,抽油杆在4700ft测量深度处已经脱离或断开。尽管采取了常规钻井测量,但由于测量没有在最初选择的深度标明任何标记,所以该公司无法确定抽油杆损坏的原因。该公司设定了新的目标,了解该系统曾发生了什么情况,以便更好的定位抽油杆引导器,最大程度地提高油井产量。
采用传统的钻井测量系统是为了确定最初抽油杆的安放位置。系统下井后,石油公司了解到采用这种90ft测量间隔的方法在此次应用中是不够的。为了克服这一局限,该公司运用了MicroGuide系统,为的是获得更高的1ft间隔分辨率的高精度测量数据。利用MicroGuide系统记录2⅜-in油管内10550ft的深度,为该石油公司提供进入扭曲段的更多洞察或领悟,包括最大可用的工具外径、以及该井真实的微狗腿的情况。使用MicroGuide系统后,该公司发现了一个大的异常。
由MWD设备提供的最初的DLS分析表明,整个这部分井段(约在4150ft之前)DLS几乎未超过1°,如图3所示(图3:传统MWD最初在4150ft之前测量的这部分井段报出DLS不到1°)。然而,仅凭DLS并不能提供井下一切情况的全貌,而MicroGuide系统还能计算侧向力。如图4所示(图4:MicroGuide测井解释了利用DLS来了解井筒状况固有的局限性,还需加上计算侧向力,才能强化之前MWD测量未捕获到的存有几处高扭曲区域的断言),在4640ft和4690ft之间明显存在额外的高扭曲区域,而这一高扭曲井段是抽油杆泵系统过早失效的根本原因。更好地了解井筒剖面能使石油公司最大程度地提高产量,延长井的寿命,而精准的井筒剖面可以通过高密度测井数据和阻塞分析来实现。由于井下设备过早的损坏、以及所导致的生产损失,作为一项额外的好处,石油公司通过避免每年需要平均三次的修井作业来实现成本节省。
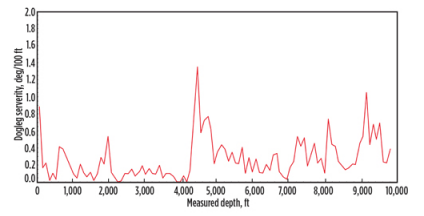
图3
另一家在俄克拉荷马州Debuhr油田的石油公司,在他的其中一部人工举升系统作业期间曾经历过持续的抽油杆引导器故障,每1个半月就不得不进行一次抽油杆断脱维修。该公司使用一个标准的抽油杆引导器设计程序,试图实现几种不同的抽油杆设计,但还是不断出现问题和多达10 次替换。进一步检查发现,严重的对抗油管的侧负载是导致抽油杆重复出现疲劳故障的原因,造成了巨大的经济损失。每次故障平均维修花费5000美元,造成长达两周的停机时间,导致每日约4桶的产量损失。为了弥补这些损失并制定一项更好的未来计划,该石油公司要求对井筒剖面和井下状况进行一次深入调查。
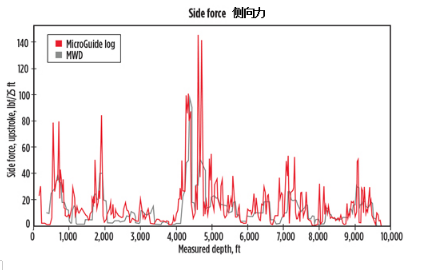
图4
最初,该石油公司只有单射孔数据,数据表明该井有一个小于1.7°的倾斜;井被假设为是垂直的,这与使用传统的MWD测得的数据结果一致。然而,使用MicroGuide系统允许以1-、5-、和25-ft的间隔进行测量,再对这些真实的高分辨率数据记录进行分析。Gyrodata服务公司发现在3000ft的测量深度有一个明显的倾斜尖峰,这在采用传统MWD测量的方法时未被探测到。在分析了MicroGuide系统的扭曲计算结果后,很明显,井筒中存在一些抗压强度和弯曲的区域。这些问题导致了抽油杆引导器在3000ft测量深度处出现疲劳故障,此处存在明显的对抗油管的侧负载。
使用MicroGuide系统,石油公司可以通过识别图5中3000ft测量深度处孤立的狗腿来获得一个更清晰和更准确的井筒状况的描述(图5:红色线代表高密度侧负载数据,数据显示了在3000ft测量深度处一个巨大的尖峰侧载荷,“与孤立的狗腿有关”,MWD设备未能检测到这一异常)。高分辨率数据改进了建模计算,从而能够开发一种新的抽油杆引导器设计。实施新设计后,该石油公司消除了与抽油杆引导器相关的故障。到目前为止,与之前相比,该系统为这家石油公司节省了超过5万美元的维修费用,每年节省修井作业时间70天,减少了生产成本损失和抽油机停机时间。
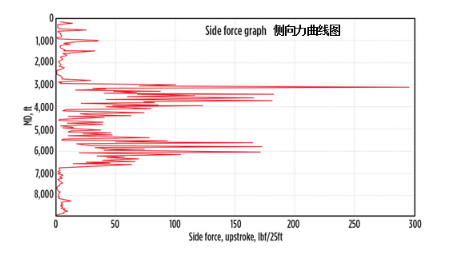
图5
能源行业将继续探讨传统设备与数字技术之间发挥协同作用的各种方式,这将改变商业模式和创新范例。在先进设备和技术的相交处,为了了解井眼中的扭曲和阻塞区域,Gyrodata服务公司已开发出一个独特的产品。由于各石油公司都试图通过结合各种其它技术组件来规划出更清晰、更精准的井下设备安置,他们会明智地考虑拥有高密度井眼测井数据的好处,以便更好的为其决策提供更具价值的信息。(文献源自Gyrodata服务公司)