压裂塞的改进正在帮助油气开采商触及新的井筒长度,同时还能缩短作业时间,降低风险。陆上和海上作业的案例研究证实,这些进步正在为石油公司节省大笔资金。当多级水力压裂从直井转至水平井时,随着水平段长度变得越来越长,加上级间间隔更密,为的是触及更多储层,因此,压裂促产作业则变得更加耗时和复杂,这带来了更高的风险问题。由于设定深度的增加,加上安装期间的预设置、更长的下入时间、以及储层压裂后快速移除压裂塞,让油气井能更快地继续进行生产等诸多挑战,因此,需要对压裂塞进行不断地改进。
完井设备供应商做出了响应,压裂塞的设计和材料构成不断地在发生着变化,为的是克服这些挑战,这源于水平段多级水力压裂的进步。图1展示了TREX Lightning Frac Plugs压裂塞,该产品克服了石油公司的这些挑战,提供了更高效且低风险的产品,使每口井最大程度低发挥其作用。这套压裂塞,从左到右依次为Lightning PLUS复合压裂塞、Lightning BOLT可溶解塞压裂塞和Lightning压裂塞。
图1
2018年12月,Packers Plus能源服务公司发布了他的TREX Lightning Frac Plugs压裂塞,见图1,这类压裂塞专门为克服石油公司的挑战而设计的,意在提供更高效且降低操作风险的产品,使每口井能获得最大效益。整个产品包括:Lightning Frac Plug压裂塞和Lightning PLUS Composite Plug复合压裂塞,这两款产品都能快速进行铣削去除,缩短了除塞时间;以及Lightning BOLT可溶解压裂塞,可溶解塞不需要进行铣削。
新一代的压裂塞设计与安装
多年来,压裂塞的长度有了明显缩短。部分产品已实现了更少部件的生产,这使得产品的可靠性得到了增强,铣削时间因材料有所减少也相应地得到了缩短。材料的改变也是压裂塞设计的一个主要变化。早期的产品由各种金属组成,导致铣削时间较长,铣削后一些大的金属碎片经常无法反流到地面。最新的压裂塞大都由各种复合材料组成。全复合材料以及设计都在不断地改进,目前,已提供了约90%的油田需求。但在高温高压环境的应用中,仍需要金属材料设计的产品,以满足环境要求。
即堵即射孔是一种完井作业固有的缓慢方法,其优点是通过携带工具起下钻的方式实施作业,然后,泵注压裂液处理地层。在直井和之后的单极计数的水平井作业中,这一操作时间并不很长;不过,随着大位移水平段变得越来越普遍以及级数达到数百个,典型的200至300 ft/min(英尺/分钟,1ft=0.3048m)的下井率会导致完井作业繁重且昂贵。
如果能够改进压裂塞的设计,使下井速度更快,石油公司就能大幅降低成本,减少压裂液的使用和缩短泵注时间。长度较短的Lightning和Lightning PLUS两型压裂塞能够快速泵入井下,典型的作业平均450至550 ft/min,线速度高达1000 ft/min。
下井时预置压裂塞是安装过程中可能出现的另一个问题。也就是说,可能会导致操作时间延长和成本增加,以及在重新恢复作业前为移除预置压裂塞而进行的设备回收的额外花费。一个预置的压裂塞也可能会影响井的后续作业,因为在找到永久性解决方案之前,为了限制另一次预置的可能性,下井速度可能会大幅降低。
一些临时的井场解决方案有时会被实施,以防压裂塞预置在老式或不可靠的塞上,但我们公司已采取了额外的设计措施来缓解这一问题。Lightning PLUS复合塞包括多个、内置于塞内的工程抗预置功能,以及线缆适配器套件(wireline adapter kit,简称WLAK)。如果将塞内的抗预置设功能与WLAK相结合,就会在压裂塞到达其计划深度之前阻止工具在拾取过程中的预启动,以及在安装过程中的预设置。
新一代压裂塞的铣削
几十年前,在直井多级压裂的早期,压裂塞由很重的材料制成且外配有铸铁滑块。与当今的压裂塞相比,这些压裂塞需要长时间铣削,而且,铣削掉的碎屑又大又重。然而,这在直井作业中不是什么问题,因为直井一般只有一个或两个压裂塞安置在井下。铣去的碎屑也不是什么大问题,因为这些碎屑只是落到井底,并不会影响当前或后续的作业。
图2
为了缩短铣削时间,缓解因碎屑引起的压裂作业问题,为多级压裂、水平井压裂开发了复合压裂塞。复合材料更轻。图2表明,复合材料比传统压裂塞的材料要轻,使用这种压裂塞有助于更快地将其泵入井下,而且,铣削时还能产生更细的碎屑,使碎屑更容易处理。Lightning和Lightning PLUS两型压裂塞的铣削时间是行业中最好的,一个井底配有马达、钻压1500 bl(680kg)的5.5 in压裂塞,平均铣削时间不到7min。
即使井内采用轻质的复合材料压裂塞,大位移水平段也使得在井的最深处对压裂塞施加足够重量进行有效研磨或铣削操作带来相当的挑战。为此,可溶解压裂塞在完井作业中正变得越来越盛行,特别是一口井的足尖级完井更具优势,Lightning BOLT可溶解压裂塞以其可预测和可靠的溶解率增强了人们使用的信心。
压裂塞的现场应用
一家在Bakken页岩作业的石油公司正寻求对一口平台批钻的井,运用拉链方式来简化其完井作业。简单地说,拉链式压裂可以提高完井作业效率,特别是像即堵即射孔这样的完井作业,也就是通过在两口井之间进行拉链式的交替作业来减少停工时间,从而提高作业效率。
例如,当一个压裂队在对一口井进行某一级压裂时,线缆服务队会在第二口井向井下下一个压裂塞,一旦压裂塞下至预定深度且射孔完毕,线缆队和压裂队会调换井位执行各自的任务。线缆队和压裂队之间这种交替作业减少了非生产时间,因为两个作业队都在持续地进行作业,而不是等待另一项工作做完再接续作业。
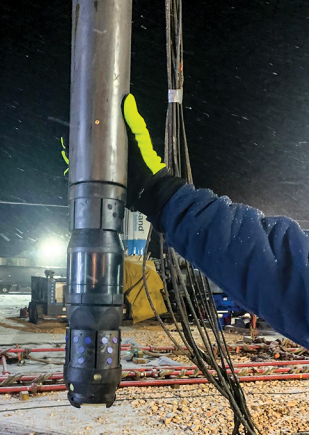
图3
拉链式压裂作业除了提高效率外,石油公司还希望优化初始回流和铣削时间,全复合压裂塞的主要好处,如图3示意的Lightning PLUS Composite Plug复合压裂塞:图3:一个Lightning PLUS复合压裂塞下井前由线缆适配器套件(WLAK)组成,压裂塞和WLAK的防预置功能阻止工具在拾取过程中预启动,以及在压裂塞到达其计划深度之前,阻止压裂塞在安装期间进行预设置。全复合压裂塞通常长度较短;因其复合材料的特性,一般铣削时间较短,压裂塞可被快速去除;较轻的铣削碎屑有助于回流和堵塞清理,特别是在与较重的材料相比时,如老式的铸铁设计;而且,重要的是复合压裂塞能提供一个经济的解决方案。在进行批钻且对多口井进行多批次多级完井时,要从市场上各种压裂塞中进行选择时,经济效益起着很大的决定性因素。
为了进一步优化其作业,该石油公司的另一个选择是在复合压裂塞上使用一个可溶解的球。可溶解球能以两种方式提高作业效率,首先,在回流操作期间,球会迅速降解,防止任何形式的井筒阻塞。第二,可溶解球可以防止铣削作业期间出现问题。例如,在铣削一个压裂塞时,它是典型的鼻部下方的底部滑脱,目的是将其推至井的下一个压裂塞。这个压裂塞的鼻部可以滑落在下一个压裂塞的隔离球上,产生一种滚珠轴承效应,这种效应可使鼻部旋转和移动,这种情况会增加铣削时间和铣削成本。可溶解球会降解到足以阻止这种滚珠轴承效应的程度,有助于加快铣削作业的进度。
随着正确的压裂塞的选择以及优化完井设计的作业得到选择,压裂即可开始。每口井的拉链式压裂都在60级左右,压裂塞下入的总深度深达20905ft,直井的下入速度超过950ft/min,水平井的下入速度超过450ft/min。所有的120个压裂塞在两口井之间被成功下井,没有出现问题或延误。压裂塞铣削最短时间3min,平均铣削时间6.5min。
另一家在德克萨斯州Midland外围Permian盆地作业的石油公司,通过在一口长井筒的足跟下入三个压裂塞,将Lightning PLUS复合塞的防预置功能运用于测试,该井的总井深约为14500ft,67级压裂。所有这三个Lightning PLUS复合压裂塞都成功地下至其计划的深度,平均下入速度约为340ft/min。压裂完成后,三个压裂塞以平均7.67min的时长被迅速铣削掉,由于复合材料的材质较轻,铣削掉的碎屑尺寸大小适当,被顺利地循环到了地面。
在墨西哥湾大陆架作业的一家海上石油公司,在另一个压裂塞无法承压后,选择了下Lightning BOLT可溶解压裂塞。因此,这些可溶解压裂塞被用来完成最后6个压裂储层,从超过17000ft的深度开始,执行了安全环保执法局要求的套管完好性测试。
在压裂塞开始下入之前,Packers Plus能源服务公司在这口井提供了他的ePLUS® Retina井监测服务系统。这一创新的实时监测系统在不干扰施工的情况下,验证了地面和井下的作业情况,运用一组传感器采集和分析井口信号,识别各种作业工况。
每个Lightning BOLT可溶解压裂塞都检测到了成功的层间封隔,而且成功地进行了促产处理。促产处治后,为了执行安全环保执法局要求的套管完好性测试,作为更低的屏障下入了一个Lightning BOLT压裂塞,并通过具有测试资质的第三方机构的验证。
虽然可溶解压裂塞目前可以完全消除铣削时间,但复合压裂塞仍占据着市场的大部分份额。在一口井里铣削50至75个复合压裂塞比铣削铸铁式压裂塞要更快,较小的铣削碎屑更易处治。而可溶解技术正在迎头赶上。这使得混合井筒设计的部署随之而增加。越来越多的石油公司在井筒的足尖段运用可溶解压裂塞,然后,在井筒的其余井段转为更多地运用传统的复合压裂塞。展望未来,如果可溶解压裂塞的市场价格继续下降,那么,采用可溶解压裂塞,将会有越来越多的水平段获得完井。这样不仅会消除铣削作业,而且,还会减少连续油管和/或修井钻机井上作业的次数和时间;减少井筒中滞留的碎屑量;节省流体和化学药品的成本;最终实现更快的周转时间,促进油气井更快的投产和创收。(文献源自Packers Plus能源服务公司)