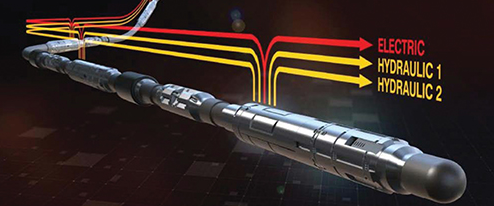
海上作业与分析数字化依赖的是部署一些能够产生某种液压操作的井下完井技术。一种通过实施混合电动数字系统的渐进式方法,是全面接受全电动方案以及与改变整个油田完井基础设施相关成本的关键所在。
通过部署能够产生大量数据的井下完井技术,可以实现海上作业与分析的数字化。尽管这些数据对于了解油藏特征和油田范围内各构造之间的相互作用至关重要,但快速响应、管理和控制井下事件的能力对数字化运营的最大化效益则更为重要。
通过整合多个来源的井下数据,以最小的控制线贯穿件,提供对井眼的快速管控,先进的油藏控制系统有助于最大限度地发挥数字化运营的优势。虽然智能完井的未来确实会严重依赖电气技术而非液压技术,但如今,利用井下监测系统和强大的数字生态系统,无论采用何种先进的油藏控制系统,石油公司或运营商们都能从利用多层次的数字化中获得受益。上图为具有集成遥测与监测架构的电动液压系统。
数字化油田的整合的必要性
今天,我们看到,数字化油田的整合和主动的油藏管理是井下高温电子设备进步与发展、以及其在永久性井下测量遥测方面取得整体成功的直接表现。早期远程驱动的液压和电动液压控制系统、以及永久性井下测量遥测技术的成功表现,提供了强大的技术支持,这些技术可加快油藏控制系统的响应,提高系统的可靠性,以及提供与其它数字油田技术的接口,同时还能提供控制更多地层的机会。
先进油藏控制系统的种类。目前油藏控制系统主要有三大类:1)液压;2)电动液压;3)全电动系统。这些系统可被视为智能完井的起始蓝图,运营商的基础设施可以确定所要部署的系统类型。此外,这些油藏控制系统可以细分为外在和内在的先进油藏控制系统。下面对这些控制系统的每一种类型做一个阐述,重点介绍一下它们成为先进油藏控制系统的能力和局限性。
液压系统。液压式油藏控制系统被广泛认为是远程驱动技术最简单的一种,迄今为止,它一直是最常见的一种控制系统。就先进的油藏控制系统而言,液压控制系统被认为是外在的,因为它们无法传输井下数据。它们是独立的系统,需要一个辅助和独立的监测系统来获得更深入的领悟。
这些系统的控制方法各不相同,但最常见的是N+1控制线配置,其中N是受控地层的数量。总体而言,液压系统有其固有的缺点,也就是必须等待控制管路加压,这反过来又会在间隔控制阀的活塞截面上发出一个力以促使换挡。虽然这种固有的设计特性在产生巨大的活塞力方面是抢进有力的,但其造成的损害在于驱动此类系统所需的时间。根据运营商的基础设施和悬挂器处导引口的数量,运营商可以利用液压式井下控制系统,以最少的地层控制数量实施完井。为了使这些系统成为外在的先进油藏控制系统,必须采用额外的点对点的井下监测系统,以提供必要的油藏生产或注入回馈。
电动液压系统。第一个电动液压系统结合了井下监测传感器,位置传感器和井下阀门驱动器,井下阀门驱动器可以通过遥测通信协议从地面选择性地对阀门进行驱动与调节。这种电动液压系统是超前开发的,这样的系统今天已被认证为是一种内在的先进油藏控制系统。
在今天的高温电子器件开发出来之前,油田开发中常会看到采用器件冗余的方法来提高电子设备的可靠性,特别是当希望设备能使用10年或更长时间时。考虑到1997年那时的电子器件在高温环境下的可靠性明显低于今天的电子器件,从事设计的工程师们决定通过将两个系统打包成一个系统来增加系统中组件的数量:一个主系统和一个备用系统。这种系统组件的增加导致了系统的总成本也随之增加,从而阻碍了系统的采用。
为了减少整个系统的组件数量和成本,开发了一种简单的电动液压外在系统,其中先进的油藏控制系统由一组无源的电气组件提供。这些电气组件不使用遥测技术,而是采用多路复用的方案来接合分布在多个井筒区域的不同间隔控制阀。外在的电动液压控制系统使用两条液压管路对间隔控制阀的动作进行控制,并且使用一条配电线路对间隔控制阀进行控制。
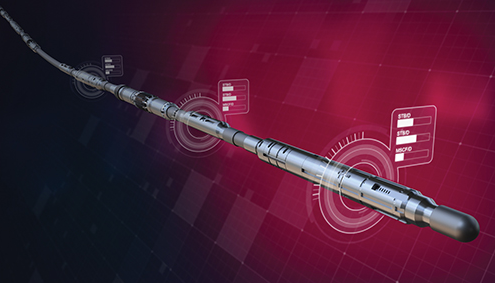
图2
所有这三条线路都连接到一个地面控制装置,当完井作业部署有间隔控制阀时,该装置能够提供选择每一个间隔控制阀所需的液压和电流。电子设备的高可靠性基本上消除了对冗余电子组件的需求,根据项目预算和目标,将冗余作为升级功能予以考虑。与全液压系统相比,内在的电动液压系统受益于更快的响应速度,而且鉴于它们与包容性监测系统共享遥测数据,因此,内在的电动液压系统可用于实施先进的油藏控制工作流程。
所有的电气系统都是先进控制系统发展的下一步。这些系统就是内在的先进油藏控制系统,因为它们已经具有了在全电动架构中多个设备之间共享的遥测数据。最近在电动机效率和功率方面的进展已使得该技术能够产生较大的能力,可以与全液压系统相媲美。这些系统通过一条单一的电热转换管路来指挥和控制多个地层,提供压力和温度方面的储层反馈,以及通过遥测到其地面设备的方式,提供完整的位置传感、虚拟流量测量和整体的系统诊断数据。
部署全电动技术时需要考虑的一个重要方面是系统保持全孔径生产或注入流量的能力。虽然引入更快的系统响应很重要,但由于间隔控制阀设计导致的流量限制可能会影响一台设备的整体潜力。当与全电动设施结合使用时,间隔控制阀的设计不再限制流量,可提供精准的阀门定位、全孔径生产或注入,以及全电动系统提供的驱动速度等优点。另一个优点是全电动系统能整合到其他类似的系统中。这样的智能完井系统,间隔控制阀和仪表不仅可以相互作用,还可与电动安全阀和其它全电动完井技术进行互动。部署兼容的全电动系统,最终的好处是它能简化中枢电缆,可以降低海上应用的整体资本支出。
虽然与内在的先进油藏控制系统相比,外在的系统在操作上更难部署,但现实情况是,外在的油藏控制系统已成功使用了20多年。通过适当级别的设计、工艺和规划,可以成功部署外部的油藏控制系统,同时也能可靠地提供必要的井眼监测和控制,目的是主动管理油藏,见图2(油藏控制系统的类型和特点)
。 运营商必须考虑井筒和油田基础设施、必要的油藏控制等级(主动与被动控制)以及系统的成本。
基于系统选择的数字化
一个完全集成的电动液压系统初步的测试和结果显示,该系统能够为越来越多的受控地层提供遥测、诊断、以及与永久性井下测量仪的整合。下一代电动液压控制系统组件依靠目前的液压间隔控制阀技术和ASIC(Application Specific Integrated Circuit特定应用集成电路)混合电路技术进行通信。模拟显示,该系统可通过一个与永久性井下测量仪共享的通用遥测协议,提供间隔控制阀定位的实时反馈。考虑到间隔控制阀流量调整设计,以及利用油管和井下环空压力和温度数据,可以实现自动化的工作流程,以快速准确的方式调整电动液压系统间隔控制阀的定位。
迄今为止,已经对这两种类型的内在系统进行了广泛的测试。在这两种类型中,全电动系统被视为是该行业长期的解决方案。一般来说,全电动数字化的概念为数字油田可能走向何方提供了一个乌托邦(空想或不切实际)式的观点,但在实践中,通过实施混合电动数字系统,一种渐进式方法是全面接受全电动系统的关键。电气化组件的长期接受度也已在多个行业得到了体现。
电动液压系统的成功实现和可靠性将会在油田全电动系统的大规模接受与使用中发挥重要作用。虽然完井效益的未来在于电动系统,但数字化不必等到这些系统成为主流时才来推进。电动液压系统是进入全电动系统的良好途径,这会使石油公司或运营商有机会利用一些现有的基础设施,同时受益于数字化油田推进所带来的完井优化。