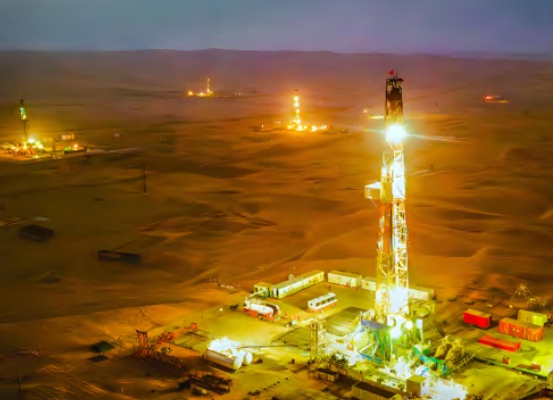
在过去的 75 年里,石油行业的陆地钻机领域经历了令人瞩目的变革。据石油技术杂志近期报道,钻井施工方法的技术改进堪称一场革命,使钻井人员从石器时代般的作业模式大步迈向太空时代般的先进水平。陆地钻机技术革新效果显著,成本大幅降低,效率得到极大提高,作业人员钻探油气的深度也实现了质的飞跃,这些都清晰地展现出陆地钻机一路走来的卓越成就。
早期陆地钻机发展历程
回溯陆地钻机的发展源头,最早的陆地钻机构造简单,材料主要是竹子和铁,动力则依靠牲畜。其采用的冲击式钻井法,是通过反复提升和下放沉重的铁钻头来完成钻孔作业。这种方式虽然能实现钻孔,但效率极低,一个钻孔任务往往需要耗费大量的人力和漫长的时间。
1859 年是陆地钻机发展的一个重要节点,埃德温・德雷克(美国第一口油井的钻凿者)在泰特斯维尔钻井时引入了蒸汽机。这一举措为钻井作业注入了新的活力,让将金属管打入地壳变得更加容易,大幅提升了作业效率。此后,陆地钻机技术持续更新。20 世纪 50 年代,柴油发动机取代蒸汽动力钻机,为钻机提供了更强劲、更稳定的动力,进一步推动了钻井效率的提升。60 年代,自升式钻机出现,这是陆地钻机发展的一座里程碑,它实现了从井架到桅杆的重大转变,让钻机在结构和功能上都有了显著进步。
进入 70 年代,现场发电机产生的电力开始应用于驱动钻机系统,这一革新为钻机的自动化和精细化操作创造了条件。与此同时,新型井下工具的问世让钻井技术向前迈出了一大步,钻井人员可以在保持钻杆旋转的同时进行定向钻井,大大提高了钻井的精准度和效率。80 年代中期,首个可转向钻井系统诞生,进一步完善了定向钻井技术,使得陆地钻机在复杂地质条件下的钻井能力显著增强。
陆地钻机的演变不仅体现在动力和钻井技术方面,操作室也发生了深刻变革。从钻台、井下到司钻房,老式手刹和脚踏板系统逐渐被触摸屏和操纵杆取代。这一变化提高了操作的便捷性和精准度,也为钻井工人营造了更舒适、安全的工作环境。
顶驱技术的陆地应用发展
在陆地钻机创新历程中,很多创新都源于海上领域,顶驱技术是其中的典型代表。20 世纪 90 年代前,顶驱技术主要应用于海上钻井,是海上钻井平台的标准配置,当时没有顶驱的海上钻机很难获得钻井合同。
随着陆地石油勘探开采的深入,顶驱技术逐渐向陆地拓展,开启了陆地钻井的新市场和新模式。哈里伯顿(H&P)公司相关人员回忆,在将顶驱技术引入陆地之前,他们已在海上钻机积累了丰富的顶驱安装和使用经验,比如安装瓦科(Varco)TD - 4 型或海事液压(Maritime Hydraulics)DDM 650 型顶驱。
当哈里伯顿(H&P)公司承接国际大型石油公司陆地钻井业务后,顶驱成为国际陆地深钻钻机合同标准,陆地深钻钻机需配备与海上相同标准的顶驱设备。但这一过程困难重重,顶驱从海上应用到陆地受到广泛质疑。
20 世纪 90 年代中期,国民油井华高(NOV)公司认为陆地钻机结构无法承受顶驱的载荷和扭矩,这一观点得到很多业内人士认同,因为陆地和海上钻机在结构和设计上差异很大,将海上顶驱技术应用于陆地钻机面临诸多技术难题。
不过,技术人员通过努力,提出并实施了一系列改进措施。比如通过在顶驱中间设置大黄梁等方式,将顶驱的载荷和扭矩有效传递到钻机底座,解决了陆地钻机结构承载问题。此外,小型封装感应电机等新型电机技术的应用,让顶驱在陆地钻机上运行更稳定、高效。
顶驱技术在陆地的应用显著提升了陆地钻井效率。立根钻井就是一个重要体现,传统钻井方式中,每次添加一根钻杆到钻柱耗时很长,而顶驱技术可将多节钻杆事先连接成立根,一次操作就能添加更多钻杆到钻柱,大大减少了因添加钻杆导致的停机频率,提高了钻井速度。
在 21 世纪初页岩热潮兴起的背景下,定向钻井技术愈发重要,顶驱技术与定向钻井技术结合,使钻井人员能更精准地控制钻头方向,在复杂地质条件下实现高效、精准的钻井作业,为页岩气等非常规能源开采提供了关键技术支持。
交流钻机的诞生与影响
交流钻机的诞生是陆地钻机发展的又一里程碑,它与机车行业交流传动技术发展密切相关。机车行业在柴油电力机车中采用交流传动技术的实践,为陆地钻机行业带来了新思路和技术借鉴,从而催生了交流钻机。
交流钻机为井场钻井带来了革命性变化,它专为井场钻井设计。在交流钻机出现前,单口油井通常依次钻探,井场钻井概念未普及,而交流钻机使从单一地点钻出多口油井成为可能,这一创新为石油开采行业带来巨大经济效益和生产效率提升。
交流钻机诞生之初不受欢迎,因其技术新颖、成本高且操作人员需掌握新技能,很多石油公司和钻井人员持怀疑态度。但随着时间推移,它展现出独特优势,对美国页岩革命产生深远影响。
哈里伯顿(H&P)公司在交流钻机发展中起重要作用。2000 年前后,公司管理层决定聚焦顶驱钻机尤其是交流顶驱钻机发展。随后几年,公司在可控硅整流器(SCR)式钻机上安装交流顶驱并推进钻机舰队改装计划。
这一过程阻力重重,公司内部很多团队成员和作业人员反对引入交流顶驱,他们认为会增加成本、停机时间,且操作人员需花大量时间学习新技能。但公司领导层积极沟通协商,努力解决问题。
通过一系列努力,公司解决了成本控制、停机时间减少和操作培训优化等问题。比如改进技术和优化管理流程降低采购和维护成本,加强技术支持和培训体系建设帮助操作人员掌握操作技能,减少停机时间。
交流钻机设计具有颠覆性,带来许多新功能和优势。精确控制是一大亮点,通过先进控制系统实现滑块控制,对钻井过程精确控制,提高效率并减少钻井事故。同时,交流钻机配备先进反馈系统,操作人员可通过触摸屏实时了解运行状态并调整参数。其驾驶室设计也很人性化,有空调和舒适座椅,与传统钻台环境相比有很大提升。
可移动钻机的发展与优势
可移动钻机是陆地钻机发展的新突破。2016 - 2022 年,可移动钻机在全球钻机舰队中的应用成果显著,使全球钻机舰队钻井周期缩短超 35%。传统钻机移位到开钻的滑移过程通常需 3 - 5 小时,可移动钻机利用先进技术将这一时间大幅缩短至 1.5 小时,提高了钻井效率和经济效益。
可移动钻机依靠液压 “支腿” 实现移动,液压 “支腿” 具有强大支撑和移动能力,可使钻机在钻井场地内移动达 500 英尺,无需额外重型运输设备。而且可移动钻机无需组装和拆卸某些部件,减少准备时间和工作量,降低设备损坏风险,提高了可靠性和使用寿命。
可移动钻机对复杂地形适应能力强,能应对不平整地面、斜坡等地形。液压 “支腿” 可根据地形自动调整,确保钻机在各种地形条件下稳定平衡,拓展了陆地钻机作业范围,使其能到达传统钻机难以到达的区域。
可移动钻机的研发综合考虑多种因素,对满足下一代非常规钻井需求至关重要。在非常规能源开采受重视的背景下,可移动钻机可使井排间距更宽,提高油井独立性和开采效率,还能在单个钻井区域布置更多排油井,提升整个区域资源开采效率。
在研发过程中,技术人员解决了诸多实际问题。比如处理好与现有井口关系,避免井口损坏,考虑泥浆管线坡度和泥浆系统重力反馈对移动距离的限制。回抽系统等创新技术的应用有效解决了这些问题,可移动钻机还考虑了井口间距和移动路径,实现对井口的灵活避让和操作,能适应美国几乎任何井场钻井地点的复杂条件。
陆地钻机的未来展望
陆地钻机未来前景广阔。机器人技术、人工智能和自动钻井将成为关键发展方向。目前,二叠纪盆地已应用机器人进行钻杆连接作业,未来机器人应用将更广泛深入。机器人可提高作业效率、稳定性和精准度,避免人为误差和事故。
自动化解决方案还能提高安全性,传统钻台存在高温、高压、机械伤害等风险,新方案可让人员从危险区域撤离,通过远程控制和监控系统管理作业,降低人员安全风险。
人工智能通过分析大量钻井数据,可预测钻井问题如地层变化、设备故障等,并提前给出解决方案,提高钻机可靠性和作业效率,减少停机时间和损失。自动钻井技术可根据预设参数和地质条件自动调整钻井过程,实现全自动化操作,需先进传感器技术和复杂算法控制系统,将提升作业效率和质量。
可持续性发展是陆地钻机领域重要方向,随着环保意识增强,具备储能能力的混合动力钻机有望成为发展趋势。混合动力钻机可在不同作业阶段灵活选择动力源,减少对传统化石能源依赖,降低碳排放,实现环保钻井作业。
未来钻井方案制定更复杂多样,需综合考虑多种因素。公司规模影响钻机选型和投资策略,大型公司倾向先进、自动化程度高的钻机,小型公司选择更经济适用的钻机。地理位置也很关键,不同地区地质、气候、环境条件不同,如寒冷地区需保暖防寒,山区需考虑运输安装,海洋附近需防腐蚀,要针对不同地理位置设计选择钻机和配套设施。
井间距、压裂间距和最佳井场规模等特性也是钻井方案重点考虑因素,随着非常规能源开采发展,合理的间距对提高资源开采效率和降低成本至关重要,最佳井场规模可优化资源配置,提高经济效益。此外,还要考虑与周边社区和环境协调发展、应对更严格环保法规和社会舆论压力等新因素。