目前,全球深水油气资源领域已成为国际著名油气公司争相开拓的新领域。尤其是2018年以来,南美洲北海岸和北美墨西哥湾等海域相继在深水获得多处重大油气勘探突破,因而更使深水油气勘探开发成为全球油气行业聚焦的“热点”。从2019年来看,全球油气新探明储量创2015年以来的新高,油气当量超过一亿桶的油气田就有26个,其中超过一半的重大发现来自于深水。
中国油气勘探开发要向深水区挺近
从我国来看,油气勘探开发向深水发展的必要性与重要性,笔者认为可以概括为“三个需要”。
油气战略接替资源的需要。油气资源直接关系到国家的能源供给和经济安全,我国迫切需要发现油气战略接替资源,但相当困难。然而,我国南海蕴藏着丰富的油气资源。整个南海盆地群石油地质资源量约230亿至300亿吨,天然气总地质资源量约16万亿立方米,占我国油气总资源量的三分之一,其中70%蕴藏于153.7万平方公里的深海,尚未得到有效开发。因此,开辟新的战略接替领域,南海深水油气资源开发已成为我国的必然选择。
充分利用国外资源的需要。目前,全球深水油气资源勘探开发蓬勃发展,方兴未艾,为我国提供了难得的利用国外资源机遇。据悉,部分油气资源国已放宽了深水油气资源对外合作的财税条款,并增加了对国际石油公司的招投标活动,这就为我国利用国外资源,创造了有利条件。例如中海油参股加拿大尼克森公司25%的圭亚那的深水区块,已连续获得重大发现,不仅在储量和产量两个方面,我国的权益均有保障,而且还可以有机会学习、积累和借鉴国外先进经验。
提高科学技术水平的需要。深水海洋环境复杂,油气勘探开发所需的技术与装备,较之浅水、近海及陆上均要求高、难度大,因而,通过深水油气勘探开发必然会驱动相关科学技术水平的提高,以我国南海深水油气田勘探开发为例,从2008年开始,国家立项“海洋深水油气田开发工程技术”,组织攻关开展科研。十多年来,已经研制出了全球领先的世界上最新第六代半潜式钻井平台“981” 等先进浮式装备,建成了以“海洋石油981”和“海洋石油201”铺管船等组成的“五型六船”深水作业船队,并自主研制成水下工程关键设备近二十套,与此同时,开发出了几十种理论模型、设计方法及其专用软件和标准指南,还建立了深水工程监测系统及试验系统十数套,从而实现了我国海洋油气工程技术与装备从300m水深到1500m的跨赿式发展,大大提高了我国深水海洋工程的科技水平。
深水油气田开发离不开水下生产系统的应用,尽管目前国内外深水油气田的开发模式因地制宜,已采用的有多种模式,诸如水下生产系统+半潜式生产平台+浮式生产储卸油装置、水下生产系统+浅水生产平台+陆上天然气处理终端、水下生产系统+FPSO等,但也是水下生产系统。因此,水下生产系统可以说是深水油气田开发的必备生产设施,我国要发展深水油气田开发,必须要掌握水下生产系统的核心技术,能够自主设计制造其关键装备。但是,目前中国与世界先进水平仍有较大差距。
中国急需研发的水下生产系统装备
气液处理设施的水下化。目前深水油气田开发采用的水下生产系统如图1所示,一般其组成为:水下井口、水下采油树、管汇系统、化学药剂注入系统、生产控制与监视系统、脐带缆、海底管道、立管等,见图1所示。
当今常规的设计方案均将液气处理设施,包括油气水分离装置、输液增压泵装置、输气堉压的压缩机装置等安装在水面设施上。但目前新的发展趋势是将其水下化,即将它们移入到水下,由水下分离器、水下增压泵、水下压缩机等组成水下油气水处理系统及海底增压系统,从而实现油气水的水下处理及外输。水下油气水处理系统将极大节省水面上设施的空间,降低对其载荷的要求,同时也将有利于提高油气田的采收率,延长油气田寿命。国外,目前巴西国家石油公司(Petrobras)已经在两个水下生产系统采用了水下增压系统来提高油气传输的压力,还在Marlim油田装设了水下油水分离及再注系统。另外,法国道道尔(Total)公司也在Pazflor油田采用了水下气液分离和增压技术,而菏兰壳牌(Shell)公司则在Perdido油田采用了水下气液分离技术。
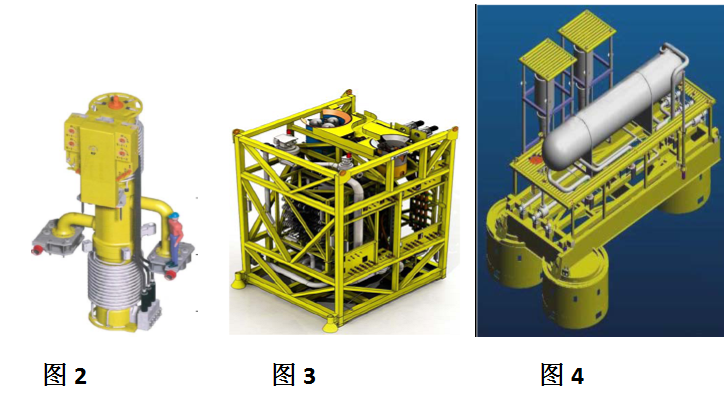
图2、图3、图4分别为水下增压泵、水下压缩机、水下气液分离器,图5为巴西Petrobras公司的水下油水分离及再注系统。
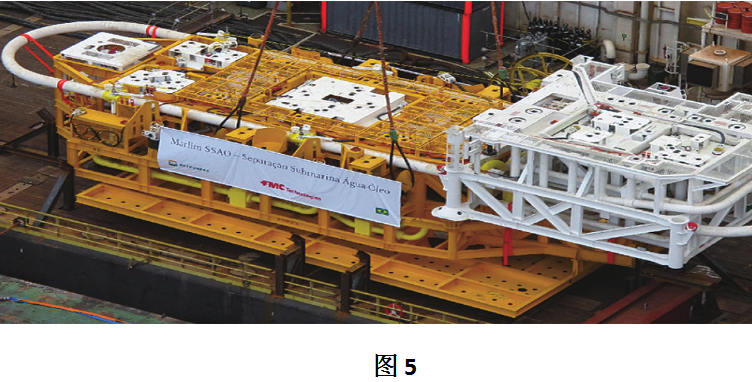
我国南海深水已建成的流花11-1油田、荔湾3-1油田和2020年新建的流花16-2油田群及2021年新建的陵水深水一号气田,虽然都应用了水下生产系统,但尚未实现气液处理设施的水下化,因此,我国应及早开展水下增压泵、压缩机、气液分离器等高质量装备的研制。
海底控制系统的全电化。传统的水下生产系统的海底控制系统均采用电液复合式控制方式,但当今的发展趋势是转向全电式控制方式。电液复合式控制需要从水面上提供液压液作为动力源,因而会带来液压液的排海对环境造成的污染,同时液压系统可能带来的任何泄漏,都会产生严重故障,并造成对海洋环境的污染,显见,缺点甚多。全电控制系统传输的是电信号,控制距离更远,响应时间更短,且无污染环境问题,还省去了控制系统中的液压组件所需的费用,減小了传输液压液管线的脐带缆的直径,极大地降低了脐带缆的费用。当然,如果同时采用液压系统作为水下生产系统的备份控制,采用冗余设计,也可进一步提高整个水下生产系统的控制系统的可靠性。
目前,全球挪威率先推行水下生产系统的海底控制系统的全电化,图6为他们研发的世界上第一座全电控制的水下采油树, 2008年已安装于挪威北海的K5F油田投产,到目前为止,运行良好。我国在这方面尚属空白,因此,高质量研制水下生产系统,需要考虑采用全电式海底控制系统,并潜心研发相关的电器元件。
供电配电设备的海底化。将原来位于水面平台上的供电配电设备安装在海底,这是水下生产系统的另一项新的发展趋势。由于大型水下气液处理装置所需功率常达几十兆瓦,传统的低压供电技术与设备已无法满足用电需求。因此,水下高压交直流供电所需要的关键电气设备包括水下变压器、水下开关等都将成为未来的研发“热点”。以水下高压断路器(自动开关)为例,国外挪威已经将其研发出的产品应用于位于北海海域 ,离岸100km平均水深885m的Ormen Lange大气田(天然气储量约3000亿方)的水下生产系统的水下压缩机的供电系统中。
近年来,挪威又开始了海底配电系统的研发,他们自2017年开始研究,目前正在海上进行测试。他们的创新理念是实施模块化,即将用于中压配电、电源转换、自动化輔助电源等设备,都安装在一个水下密闭罩中,形成一个海底模块化的配电系统,直接驱动海底的泵、压缩机以及其它工艺设备。这样即可省去传统的自水上平台为每台设备单独配备的电缆,而且配电系统距离供电设备也近,可以节约大量投资。目前研发的海底配电系统可以提供高达100兆瓦(MW)的电力,并可在600公里范围内供电,它可用于超深水3000米水深,并确保工作30年无需维修。正由于这些条件的极其苛刻,可靠性的要求也非常严格,因而该配电系统中包括海底控制系统、不同电压配电系统、海底不同电压开关设备以及海底不同电压变速驱动器等组件,均需重新设计、研制,再加上海上全尺寸的测试,包括温度、振动、压力测试及加速寿命测试等,既要严格按照规范标准,又要保证数据精准,困难大,费时多,故研发成功尚需时日,预计2023年在国外可投入使用。图7为挪威Aker公司近年研制的用于Ormen Lange气田深水水下供电设备断路器,图8为该公司正在研发的模块化配电系统。我国目前尚属空白,需要自主研制这些高质量水下供电配电电器。
水下通信系统的最优化。这里所说的最优化指的是要与时俱进,跟上现代的步伐,采用当今最先进的技术与装备。首先,由于现代通信要求系统的各个接口要实现标准化, 这样才有利于第三方设备的接入,使得整个通信系统的可扩展性大大增强。因此,对于水下生产系统来说,其通信接口包括水下主控站 (MCS)与分散式控制系统(DCS)的通信接口、 水下各种监测仪表的通信接口、水下控制系统的水面上设备与水下设备的通信接口等,都要实现标准化,以满足现代通信的要求。
其次,由于现代通信要求带宽大,而光纤通信带宽大,已逐渐取代电力载波,成为当今主要信号传输方式。而水下生产系统目前应用的各种监测和检测仪表以及井底仪表赿来赿多,且对信息传输的要求不断增加,再加上油气田生产优化也要求它将水下各种数据尽快传到水面上来,因此,采用光纤通信,扩大通信带宽,应用以太网,已成为当今水下生产系统通信系统的发展趋势。总之,这些现代通信的最优化要求,我国的深水水下生产系统的通信系统均应满足。
综合上述,我国需要大力发展深水油气田的勘探开发,而水下生产系统以其高适应性、高经济性成为深水油气田开发模式中必不可缺的组成部分,因此,高质量研制水下生产系统己成为我国开发深水油气田的一项重要任务。